Key Challenges in Managing a Multigenerational Workforce in Manufacturing
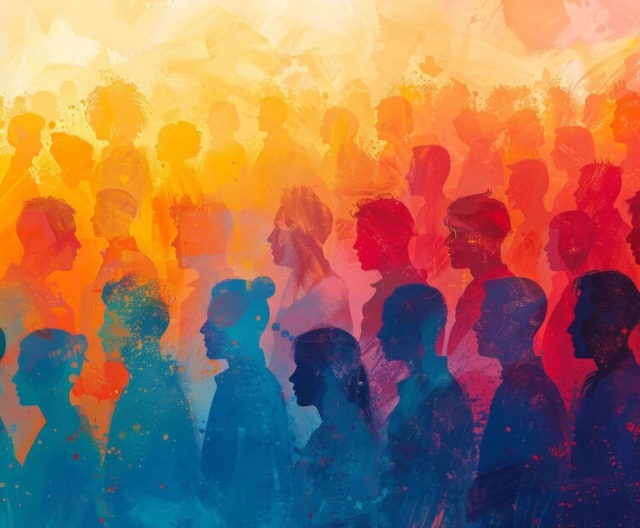
May 22, 2025
Key takeaways Vietnam’s manufacturing faces critical talent crisis: 70% of Gen Z avoid manufacturing roles while 30% of workers approach retirement. Generational workplace conflicts affect 75% of Vietnamese employees, directly impacting productivity and operational efficiency. Two-way mentoring and flexible policies successfully address generational diversity challenges across all age groups Proactive multigenerational management transforms potential disruption […]
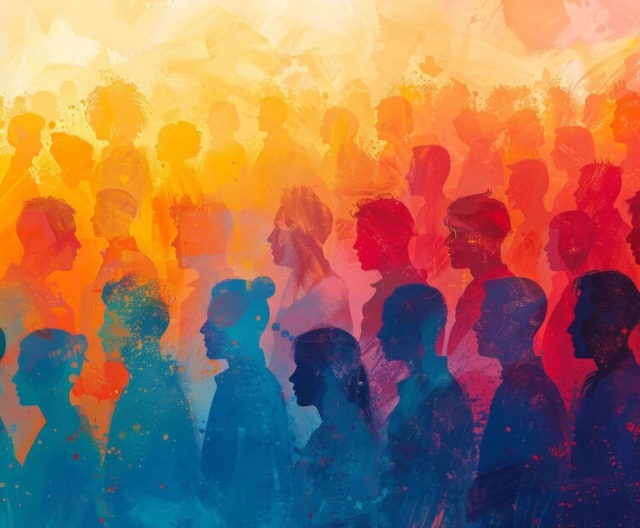
Key takeaways
- Vietnam’s manufacturing faces critical talent crisis: 70% of Gen Z avoid manufacturing roles while 30% of workers approach retirement.
- Generational workplace conflicts affect 75% of Vietnamese employees, directly impacting productivity and operational efficiency.
- Two-way mentoring and flexible policies successfully address generational diversity challenges across all age groups
- Proactive multigenerational management transforms potential disruption into measurable competitive advantages.
Manufacturing leaders across Vietnam and Southeast Asia face workforce transformation unlike anything previous generations encountered. Five generations now work side by side—from Traditionalists to Gen Z—and companies must handle conflicting work styles, communication preferences, and career expectations while maintaining productivity and safety standards. Successfully navigating these multigenerational workforce challenges determines which organizations thrive in today’s competitive landscape.
Generational diversity in today’s manufacturing workforce
The demographic foundation of manufacturing has shifted faster than most CEOs anticipated, fundamentally altering talent supply chains and workforce dynamics across Southeast Asia.
Current workforce composition reveals three critical trends:
- Gen Z workforce acceleration: According to an Anphabe survey of 750 Vietnamese companies, Gen Z already represents 30% of the current workforce and continues growing rapidly. These employees enter manufacturing with completely different expectations—seeking purpose-driven work, fast career growth, and flexible environments rather than traditional long-term job stability.
- Imminent retirement exodus: With 30% of manufacturing workers over 55, companies face what experts call a “silver tsunami” of retirements. These departing employees take decades of specialized knowledge, technical skills, and company memory with them. The World Economic Forum warns this could leave 2.1 million manufacturing positions unfilled by 2030 if companies don’t act.
- Complementary generational strengths: Baby Boomers and Gen X offer deep industry knowledge and process expertise, while Millennials and Gen Z contribute digital skills and innovative thinking. The challenge is creating synergy rather than conflict between these different skill sets.
Understanding how Gen Z is shaping the future of work becomes crucial for manufacturers seeking to attract and retain this emerging talent pool. The convergence of demographic change and technology advancement means manufacturing companies must simultaneously prepare for knowledge transfer from retiring experts while adapting to the expectations of digitally native younger workers.
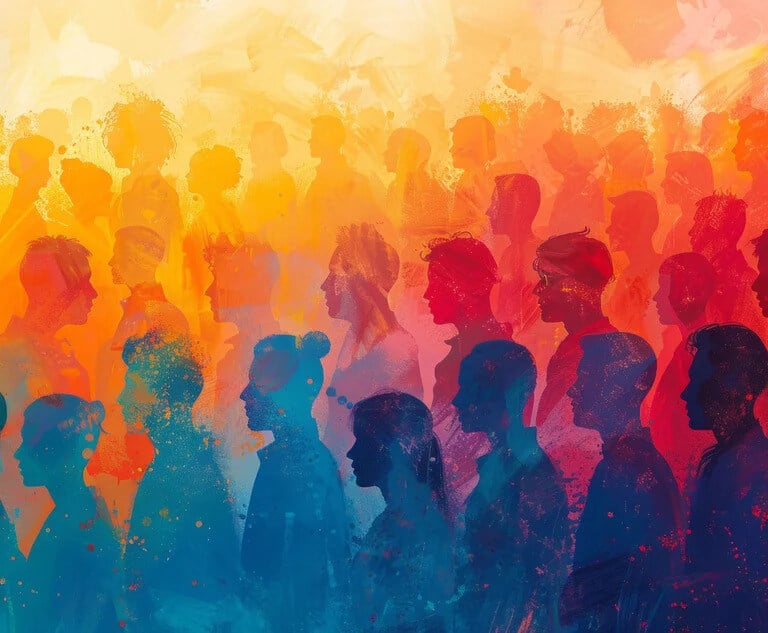
Critical challenges of managing a multigenerational workforce
These generational differences translate into measurable business risks that directly impact operational efficiency, talent costs, and competitive positioning in ways many leaders underestimate.
Talent attraction and retention crisis
The numbers reveal a harsh reality that demands immediate attention. Ms. Cao Thị Minh Trang, HR Director at Schneider Electric Vietnam, observed a fundamental disconnect: “While the older generation sees young people as lacking the patience and commitment for the long haul, Gen Z believes that working at a place for more than two years is too long.”
This creates a retention nightmare. Schneider Electric discovered that over 20% of their Gen Z workforce resigned annually because young employees “didn’t enjoy the work” and viewed staying more than two years as “too long.” The retention crisis goes beyond individual dissatisfaction. Research shows the average Gen Z employee stays just 2.2 years, creating constant recruitment and training costs that directly hurt operational efficiency.
When combined with retiring experienced workers, companies face a double talent drain that threatens both current operations and future capabilities. This isn’t just about filling positions—it’s about maintaining the knowledge and skills that keep manufacturing operations running smoothly. The misunderstanding between team leaders and Gen Z employees often amplifies these retention challenges.
Communication and cultural conflicts
Research reveals that 75% of Vietnamese employees experience generational conflicts at work, stemming from fundamental differences in communication styles, hierarchy expectations, and feedback preferences. These conflicts create measurable productivity barriers that extend far beyond interpersonal tensions.
The communication disconnect manifests in three key areas:
- Hierarchy expectations: Younger workers expect collaborative, informal environments where they can voice ideas freely, while older employees value structured hierarchies and formal communication channels.
- Feedback frequency: Gen Z and Millennials crave regular feedback and coaching, contrasting with traditional periodic performance reviews preferred by older generations.
- Information sharing methods: Digital natives prefer instant messaging and collaborative platforms, while experienced workers rely on face-to-face discussions and formal documentation.
Gen Z hires often feel uncomfortable in traditional corporate environments with strict procedures. Manufacturing environments amplify these challenges because coordination and safety depend on clear, consistent communication protocols.
When generational communication styles clash, the results affect productivity, workplace safety, and quality standards. Poor communication between generations leads to mistakes, accidents, and inefficient processes that directly impact the bottom line.
Skills gap amplified by technology
The intersection of generational differences and technological change creates a complex skills challenge that requires strategic action. The World Economic Forum projects that 50% of manufacturing roles will require new tech skills by 2025. Yet research shows that 59% of manufacturers lack structured retraining programs to address this gap.
This creates a paradox: older workers have deep industry knowledge but may struggle with digital tools, while younger employees are tech-savvy but lack practical manufacturing experience. Without deliberate intervention, this skills mismatch will worsen as Industry 4.0 technologies become standard across manufacturing operations.
The problem extends beyond individual capabilities. Companies that can’t bridge this skills gap will struggle to adopt new technologies, maintain competitive efficiency, and attract the talent they need for future growth. Implementing inclusive learning and development programs becomes essential for addressing these challenges.
Strategic solutions for successful multigenerational workforce management
Forward-thinking manufacturing companies are proving that proactive intervention transforms generational friction into measurable competitive advantages through targeted strategies that address root causes rather than symptoms.
Implement bidirectional mentoring programs
The most successful companies have moved beyond traditional one-way mentoring to create two-way knowledge exchange. Schneider Electric Vietnam pioneered “reverse mentoring,” pairing Gen Z employees as mentors to senior executives on technology and social media trends, while experienced workers share industry knowledge and technical expertise.
This approach solves multiple problems at once. It ensures critical knowledge transfer before senior employees retire, while also giving younger workers the recognition and growth opportunities they want. This “multi-colored” workforce approach has helped their company maintain low conflict and high engagement across generations.
The key is making it formal. Successful programs require structured pairing, clear objectives, and regular progress reviews to ensure both parties benefit from the exchange. Companies that implement formal reverse mentoring see improved knowledge retention, better technology adoption, and stronger relationships between age groups. Understanding how to refresh perspectives with Gen Z can enhance these mentoring relationships.
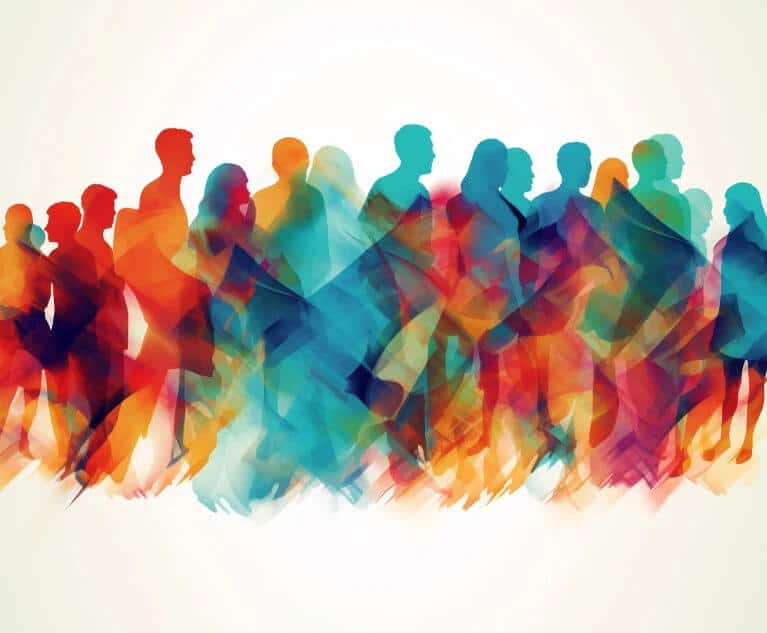
Create flexible work arrangements within manufacturing constraints
Despite traditional manufacturing limitations, innovative companies find creative flexibility solutions that meet diverse generational needs without compromising operations. The key is understanding that flexibility doesn’t mean abandoning operational discipline—it means strategic adaptation.
Successful flexibility strategies include:
- Baby Boomers and Gen X: Phased retirement options and reduced hours through part-time consulting roles and knowledge transfer positions that maintain their expertise while easing transition
- Millennials: Work-life balance focus with compressed work weeks, enhanced family leave policies, and scheduling that accommodates family responsibilities
- Gen Z: Schedule control and purpose alignment through flexible shift timing, involvement in sustainability initiatives, and roles that clearly connect to company mission
Schneider Electric introduced flexible scheduling and “recharge” breaks for tenured employees, recognizing that different generations value different types of flexibility. DKSH Vietnam demonstrates another approach by personalizing benefits packages—providing family healthcare support for older staff and education and wellness programs that appeal to younger employees.
This customization acknowledges that one-size-fits-all approaches fail to engage a diverse workforce effectively. Companies that successfully implement flexible policies see improved retention across all age groups and measurably higher employee satisfaction scores.
Develop clear, multi-track career pathways
Career development represents the most critical intervention point for multigenerational workforce management, with clear pathways serving as both retention tools and succession planning mechanisms.
The career pathway gap creates competitive disadvantage:
- Only 29% of local Vietnamese manufacturing firms have formal career pathways compared to 45% of foreign-invested companies
- This 16-percentage-point gap directly correlates with higher turnover rates across all generations
- Companies without clear advancement routes struggle to retain both ambitious young workers and experienced employees seeking growth
Successful companies create multiple advancement tracks that recognize different career aspirations and life stages. Technical expert paths appeal to employees who want to deepen specialized knowledge, while management tracks attract those seeking leadership responsibilities. This dual-pathway approach addresses the rapid progression expectations of younger workers while providing growth options for experienced employees who prefer contributing as individual contributors.
Implementation requires clear communication about advancement criteria, regular career discussions, and visible examples of employees who have successfully progressed through different pathways. Companies with transparent career paths report significantly higher retention rates and better employee engagement across all age groups.
Manufacturing executives who master multigenerational workforce challenges will secure decisive competitive advantages in Southeast Asia’s evolving landscape. Companies that recognize Gen Z workers’ unique motivations while balancing all generational needs transform demographic disruption into innovation engines. Contact Talentnet’s expert HR consulting team to develop targeted strategies that turn your generational diversity into sustainable competitive advantage.
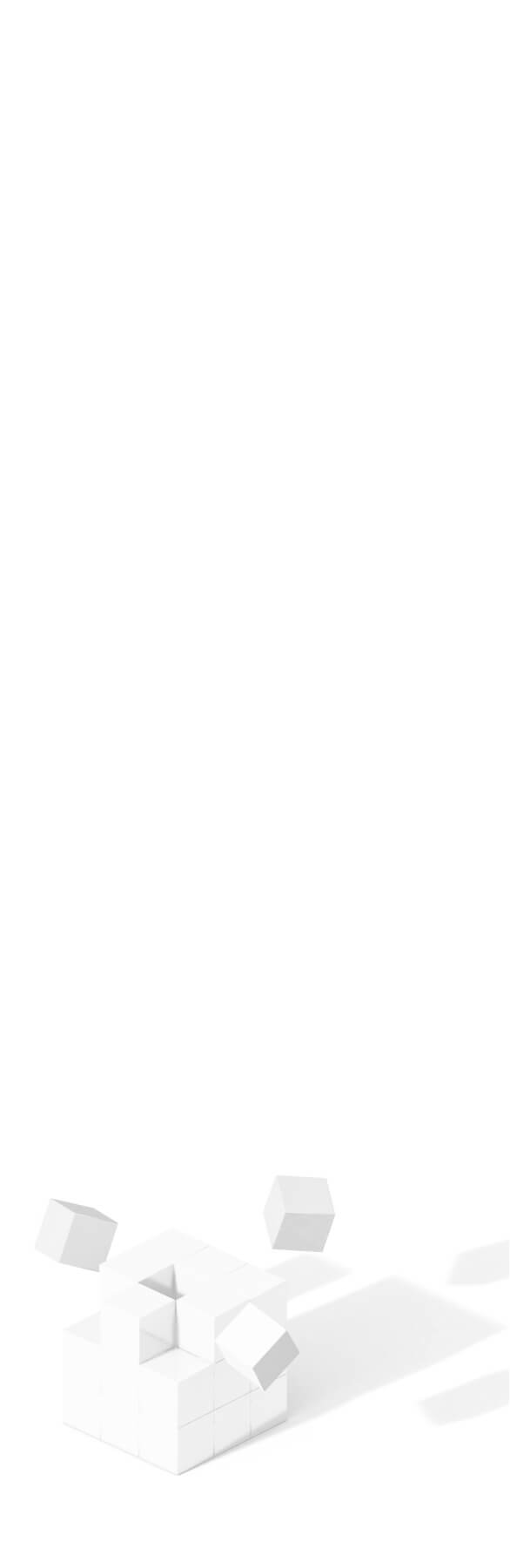
Solve your HR problems!
6th Floor, Star Building, 33 Mac Dinh Chi, District 1, Ho Chi Minh City, Vietnam