Leadership Training for Manufacturing Supervisors: The Strategic Role of HR in Driving Lean Success
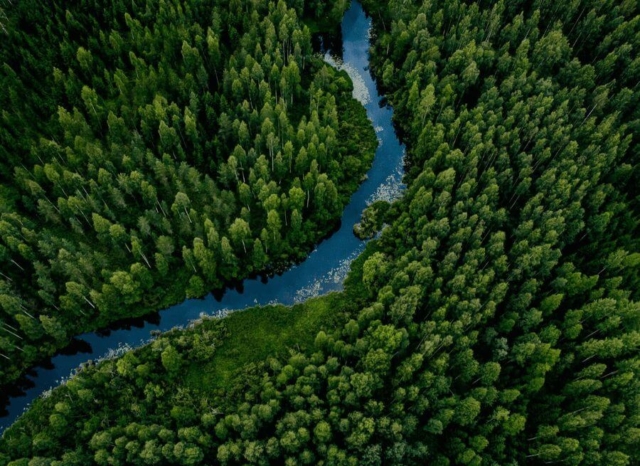
May 21, 2025
Vietnamese manufacturing businesses are missing out on millions in potential profits. Despite employing nearly 12 million people, according to Vietnam's General Statistics Office, only 10-15% of manufacturers worldwide use lean methods effectively. This creates a huge opportunity for leaders who understand that lean transformation succeeds only when leadership training for manufacturing supervisors supports the human side of change.
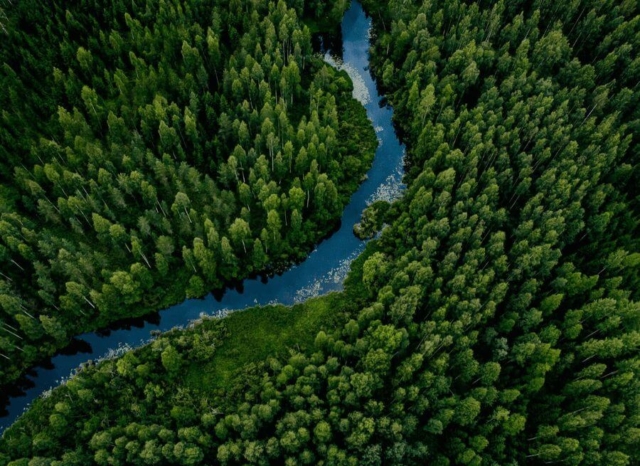
Key takeaways
- Companies using lean methods with strong leadership training for manufacturing supervisors see productivity gains over 40% without major capital investment.
- Poor workforce strategies cost manufacturers $10,000-$40,000 per skilled worker replacement due to high turnover.
- HR must be involved from day one of lean transformation to align talent, build training programs, and manage culture change for sustainable results.
Manufacturing faces a critical moment where operational excellence and workforce strategy must work together. With 60% of manufacturers saying talent retention is their top priority and lean showing proven productivity gains over 40%, the question isn’t whether to pursue lean transformation—it’s how to make your people strategy drive maximum impact through effective leadership in the manufacturing industry.
Current workplace dynamics demand strategic HR leadership
Three fundamental workforce challenges now threaten every manufacturing company’s ability to compete effectively, creating an urgent need for HR leadership that goes far beyond traditional personnel management.
Skills gaps threaten lean implementation success
Vietnam’s manufacturing faces a serious skills problem. According to Vietnam’s General Statistics Office, only 27% of Vietnamese workers have formal training certificates, leaving about 38 million workers without the skills needed for modern manufacturing. This gap becomes worse during lean transformations, which need workers who can solve problems, think about continuous improvement, and make decisions based on data.
The Vietnamese government recognizes this threat to competitiveness and is considering an Investment Support Fund to cover up to 50% of worker training costs. Companies trying lean without fixing these basic skill problems often see their improvement efforts fail during implementation. Workers who aren’t ready for standardized work, visual management systems, or team problem-solving can’t maintain the behavior changes that lean requires.
Turnover costs exceed lean investment returns
The math on workforce instability presents a stark challenge to lean ROI. According to a 2024 manufacturing HR study, replacing one skilled frontline worker costs between $10,000-$40,000, with 56% of HR leaders saying turnover creates moderate to severe impact on profits. In the U.S. manufacturing sector, 4.7 million workers left their jobs in 2023—about one-third of the industry’s workforce.
This turnover crisis hurts lean transformation in multiple ways:
- Departing employees take process knowledge and improvement ideas with them
- New hires need extensive retraining on standardized work procedures
- Teams lose the stability needed for continuous improvement culture to develop
- Each departure can cost more than most lean improvement projects
Productivity stagnation reveals deeper problems
Manufacturing productivity data shows the cost of ignoring workforce development. According to industry reports, U.S. manufacturing labor productivity grew only about 0.5% annually from 2015-2020—barely one-third of economy-wide productivity growth. This poor performance happens despite major technology investments, suggesting the limiting factor isn’t equipment capability but workforce engagement and process optimization.
Lean methodology directly addresses this productivity gap by empowering workers to eliminate waste and improve processes. However, without HR systems that select, develop, and keep employees capable of continuous improvement thinking, lean tools remain underused.
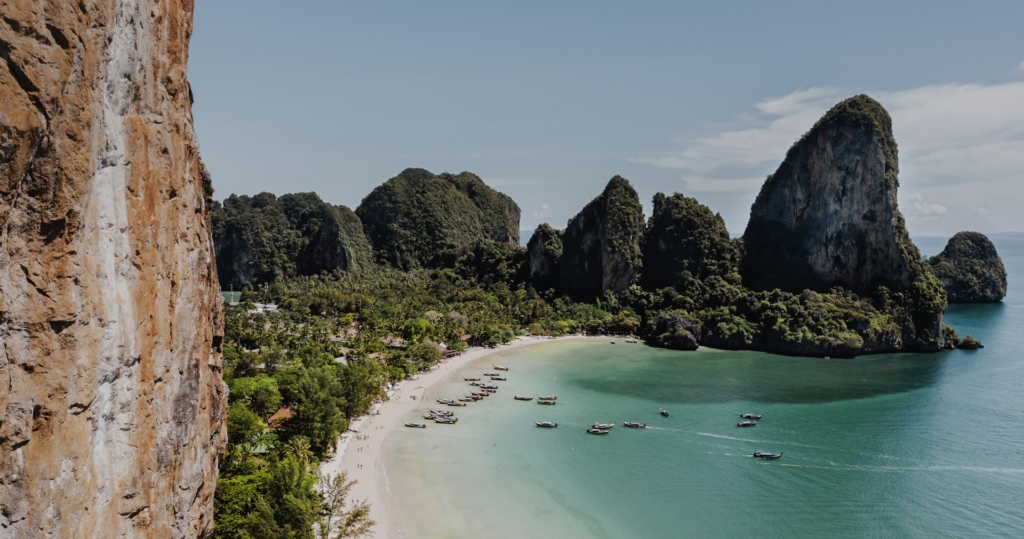
Leadership development drives lean transformation success
Real-world evidence from manufacturing companies across global markets proves that HR-driven leadership training for manufacturing supervisors creates measurable competitive advantages that sustain long after initial lean implementation.
Vietnamese success stories show HR impact
Vietnam Precision Machining, a mid-sized company in Bac Giang serving foreign investment and export markets, achieved remarkable results through HR-supported lean transformation:
- Operating profit: +50%
- Labor productivity: +25%
- Machine productivity: +15%
- Leadership capability scores: +25%
This case demonstrates how organizational leadership and culture alignment drives transformation success. The company didn’t just change processes—they changed how people thought about their work and their ability to improve it through targeted identifying future leaders talent acquisition strategic success.
Global examples validate people-focused approaches
Nike’s lean supply chain initiative shows how HR-driven training spreads lean knowledge across complex supplier networks. Through Nike’s dedicated lean training center in Vietnam, 80% of the company’s footwear manufacturing partners adopted Nike’s lean production system. This resulted in higher productivity, fewer defects, and shorter product lead times.
Danaher Corporation provides perhaps the most compelling long-term evidence of HR-lean integration. Their Danaher Business System (DBS) is built on Kaizen continuous improvement principles with HR playing a central role in culture development. According to company reports, DBS enabled Danaher to integrate over 50 acquisitions while achieving about 30% annual profit growth and an 80,000% increase in market value since the 1980s.
Expert insights confirm strategic necessity
Industry leaders consistently emphasize HR’s critical role in successful transformations. Suhail Bin Tarraf, CEO of Tanfeeth, who led a large-scale lean turnaround, notes: “In transforming our organization, we found that it was hard to overestimate the need for HR support at every level. It really was crucial to the transformation’s success.”
Kathi Hanley, former Toyota HR Manager and lean coach, reinforces this view: “Employee selection, compensation, promotion, and retention practices—all typically in HR’s wheelhouse—need to support the transformation to a lean enterprise. Often we see traditional HR systems failing to promote the behaviors needed for lean.”
Actionable strategies for HR-driven lean success
Four proven implementation strategies enable manufacturing leaders to align HR capabilities with lean transformation goals while building the organizational foundation needed for long-term competitive advantage.
Embed lean principles in talent management systems
HR departments must redesign core people processes to reinforce lean behaviors. This means hiring and promoting problem-solving ability and teamwork, not just technical skills. Job descriptions for manufacturing roles should clearly emphasize continuous improvement responsibilities, while performance management system evaluations and promotion criteria must include lean behaviors such as team-based problem solving and Kaizen participation.
Companies implementing this approach make specific changes to their talent management:
- Adjust compensation plans to include team bonuses for quality or waste-reduction targets
- Modify promotion pathways to value leadership in improvement projects
- Design interview processes that test collaborative problem-solving abilities
- Create career development paths that reward continuous improvement contributions
Effective implementation requires performance management system alignment that measures and rewards lean behaviors consistently across all organizational levels.
Invest in comprehensive training and leadership development
Successful lean transformations require multi-level training programs—from basic lean awareness for all employees to advanced continuous improvement certification for lean champions. This is where leadership training work becomes evident through measurable results. Many leading firms establish internal “Lean Academies” or partner with consultants to develop internal expertise rapidly.
The Vietnam Association for Supporting Industries (VASI) Lean Transformation Network, launched in 2022, demonstrates this approach at scale. Starting with five pilot enterprises, the program promotes shared learning with HR and training experts guiding cross-company Kaizen projects. According to VASI reports, participating factories achieved over 20% annual efficiency improvements.
Leadership training proves especially critical, as mid-level managers must learn coaching and facilitation skills rather than command-and-control approaches. Understanding individual Emergenetics test profiles helps tailor training approaches to different thinking styles and behavioral preferences. Cross-training workers for multiple skills increases operational flexibility while engaging employees in continuous learning that improves retention.
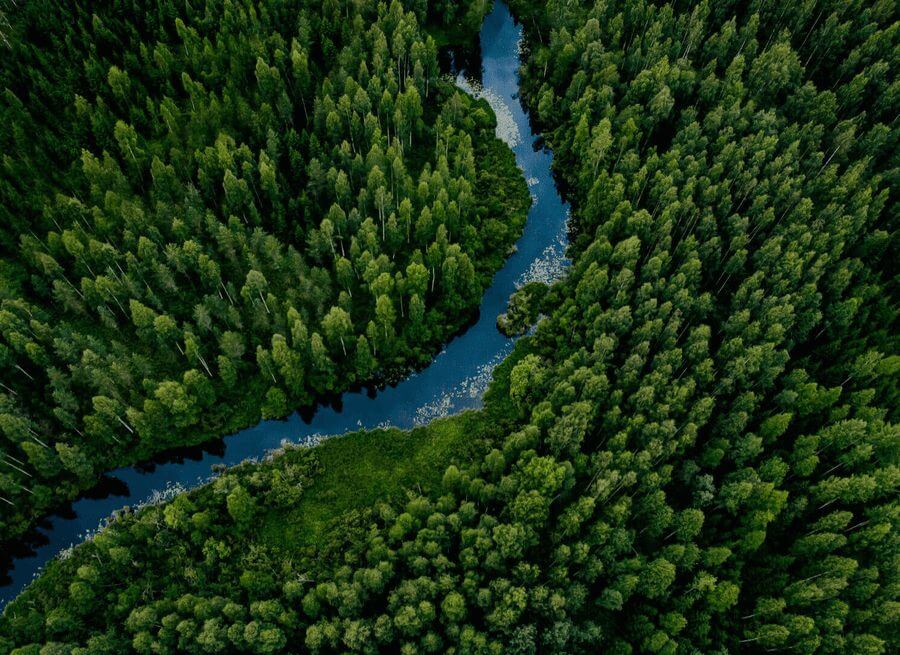
The 2023-2025 period sees manufacturers pursuing “Lean 4.0″—merging lean practices with Industry 4.0 technologies and sustainability goals. HR departments must ensure workforces are trained for IoT, data analytics, and automation while maintaining lean’s human-centered improvement culture.
This evolution requires HR to balance traditional lean principles with emerging workforce needs. Environmental training now integrates with lean workshops to build capability for the combined “lean-digital-green” transformation model increasingly demanded by customers and regulators. The challenge lies in recruiting tech-savvy talent while providing digital training to existing production staff, often requiring succession planning to ensure knowledge transfer and continuity.
Form dedicated teams and ensure cultural alignment
HR should work with senior management to establish dedicated lean transformation teams staffed with high-potential individuals. Carlos Zuleta Londoño, COO of Porvenir, noted: “Committing to lean management means making a few sacrifices. One of the most important ones we made was to staff the lean team only with A players—in fact, the head of that team was one of my best managers.”
Cultural change management represents perhaps HR’s most critical contribution. According to Gartner’s 2024 HR Survey, over half of HR professionals cite organizational cultural resistance as a top challenge. Different organizational culture and leadership styles require tailored approaches to change management. HR must champion transparent communication, address fears about job security, and align all policies from meetings to conflict resolution with lean’s collaborative problem-solving emphasis.
The evidence clearly shows that HR’s strategic involvement in leadership training for manufacturing supervisors determines lean transformation outcomes. Companies with aligned workforce strategies achieve dramatic productivity gains while those treating HR as secondary struggle with implementation and sustainability. As manufacturing faces demographic shifts, skills shortages, and digital integration demands, organizations that embed lean principles into their talent management systems through expert HR consulting services will capture competitive advantages their competitors cannot easily copy.
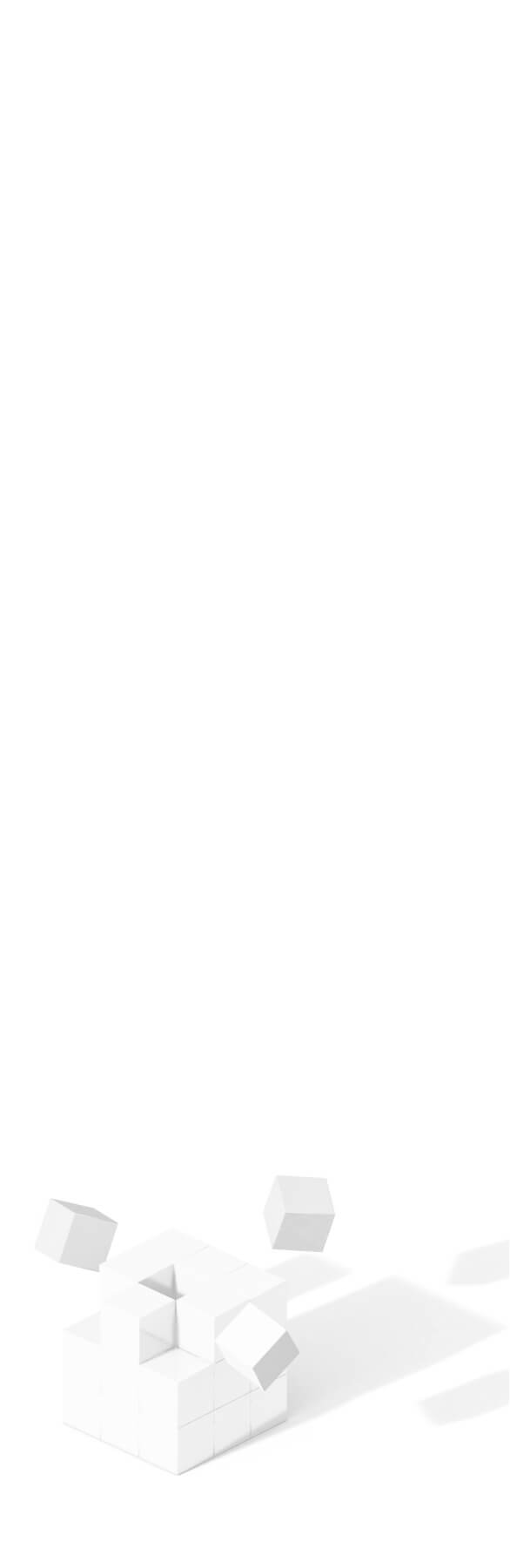
Solve your HR problems!
6th Floor, Star Building, 33 Mac Dinh Chi, District 1, Ho Chi Minh City, Vietnam