How Vietnamese Manufacturers Can Develop the Next Generation of Industry Leaders

May 21, 2025
Vietnam's manufacturing sector drives the nation's economy, contributing 40% of GDP and powering export growth. But a serious threat is building beneath this success story. According to International Labour Organization data, 2.1 million manufacturing jobs could remain unfilled by 2030. This isn't just a hiring problem—it's a next generation leader crisis. With most family business owners over 50 and planning to retire soon, the leadership gap is approaching faster than most CEOs realize. Companies that build strong leadership pipelines now will dominate tomorrow's market.

Key Takeaways
- Vietnam faces a potential 2.1 million manufacturing worker shortage by 2030, creating an urgent next generation leader crisis that threatens business continuity and competitive advantage.
- Only 20% of Vietnamese family businesses manage leadership transitions successfully, while 70% of job applicants lack basic technical skills needed for next generation manufacturing roles.
- Digital transformation will change half of all manufacturing jobs by 2025, yet most companies lack next generation manufacturing investment programmes to prepare their workforce for these new requirements.
- Young talent development becomes critical as Gen Z workers actively avoid manufacturing careers, requiring companies to modernize their workplace culture and career development approaches.
- Proven strategies like structured succession planning, mentorship programs, and strategic talent partnerships can build strong leadership pipelines for leadership in manufacturing excellence.
Building the next generation leader has become a critical business need for Vietnamese manufacturers. The combination of an aging workforce, rapid digital change, and shifting worker expectations creates challenges that demand immediate CEO attention. This analysis shows the specific problems threatening your leadership pipeline and provides proven strategies to build the leadership strength needed for long-term competitive success in leadership in manufacturing.
The escalating leadership crisis directly impacts your business
This crisis hits your bottom line through three interconnected failures: succession gaps that paralyze decision-making, skill deficits that limit productivity, and engagement problems that drain talent and resources.
The next generation leader succession crisis isn’t a future problem—it’s happening now and directly threatens your company’s ability to execute strategy and maintain operations. |
Critical succession gaps threaten continuity
The succession crisis runs deeper than simple retirement statistics. According to EY research, 58% of family business owners are over 50, with 35% planning to retire by 2025. Yet more than 40% of these businesses have no clear successor in place. This creates a dangerous leadership vacuum that threatens decades of built value.
The problem extends beyond family businesses. Deloitte research shows that:
- 56% of organizations in Vietnam struggle to find enough leaders
- 66% say the quality of available leaders is poor
- Only 20% of Vietnamese family firms manage succession smoothly
When you combine coming retirements with weak succession planning, you get a crisis that can destroy operational continuity and strategic execution. The rest often face succession crises that can wipe out years of growth and market position.
Pervasive skill deficits hinder performance
The talent crisis goes beyond numbers to quality problems that hurt performance right now. A ManpowerGroup-ILSSA survey found that 21% of manufacturing businesses struggle to fill skilled roles. Even worse, 70% of employers report that job candidates don’t meet basic technical requirements for next generation manufacturing positions.
This skills gap creates immediate productivity problems and limits growth potential. The World Economic Forum warns that 50% of manufacturing roles will need new technology skills by 2025, yet 59% of manufacturers have no programs to retrain their workers. This gap between what companies need and what they’re doing to prepare threatens competitive position as Industry 4.0 technologies reshape operations.
Disengagement and turnover erode your bottom line
Employee engagement directly affects your ability to build future leaders, and the current situation is costly. According to Manufacturing Institute research, only 25% of manufacturing employees worldwide are truly engaged in their work.
The financial impact is severe:
- 81% higher absenteeism rates
- Increased quality problems
- Productivity drops of approximately 23%
- $50,000 replacement cost per departing employee
A 2025 Vietnam survey confirms these concerns, showing that 65% of foreign-invested manufacturers and 64% of local manufacturers cite keeping good employees as a major challenge. High turnover rates drain resources while weakening your future leadership bench.
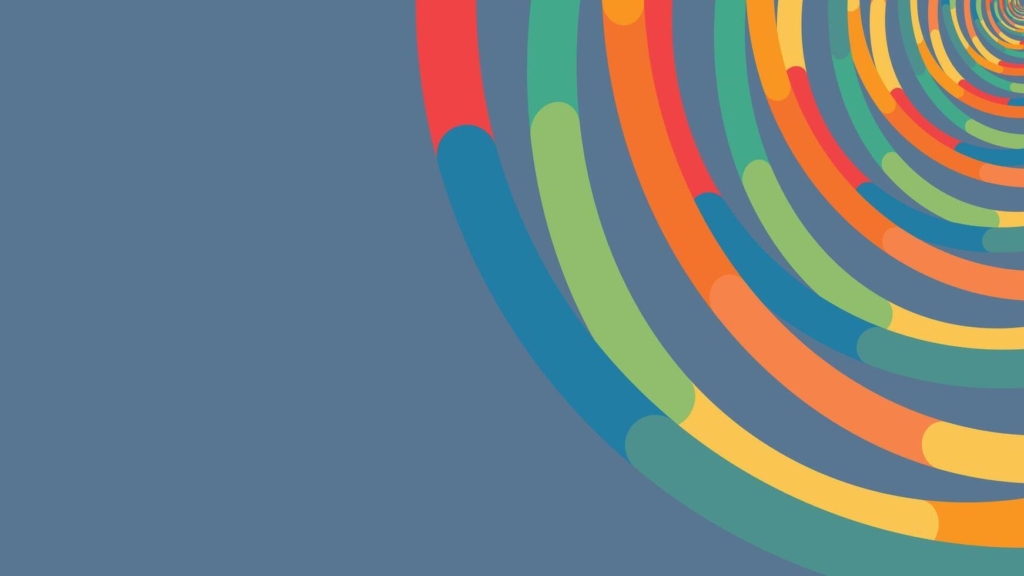
Key roadblocks to developing future manufacturing leaders
Four fundamental barriers block effective young talent development, each requiring different strategic responses to overcome their impact on your talent pipeline.
An aging workforce creates an experience vacuum
Vietnam’s population reality creates a massive knowledge transfer challenge. International Labour Organization data shows that Vietnam has one of the fastest-aging workforces in Asia, with 25% of manufacturing workers now over 55. This aging trend speeds up the timeline for leadership development, as critical company knowledge walks out the door with retiring experts.
The experience loss becomes particularly serious because many first-generation business owners haven’t formally identified or trained successors. Traditional Vietnamese business practices often center decision-making around founding leaders, making knowledge transfer more complex than simple documentation can solve.
Digital transformation demands evolving skillsets
Fast technological change fundamentally alters what leaders need to know in manufacturing. An HR Consulting firm observes that “65 per cent of all jobs that Gen Z will do do not exist yet and nearly 50 per cent of all roles in manufacturing will need to change within the next 3–5 years as the industry becomes fully digital.’
This technological shift creates a skills gap where current managers lack experience in:
- Change management for digital transitions
- Data analysis and interpretation
- Automation oversight and optimization
- Cross-functional technology integration
Bui Ton Hien, Director of the Institute of Labour Science and Social Affairs, notes that automation “will strongly affect the demand for skilled workforce in the labour market within the next 2–3 years.“
Gen Z workforce expectations require adaptation
Generational changes present both opportunities and challenges for young talent development. By 2025, about one-third of Vietnam’s workforce will be Gen Z workers. But Anphabe research shows that 70% of Gen Z actively avoid manufacturing jobs, preferring service sector opportunities that offer better work-life balance and modern work environments.
This reluctance comes from a mismatch between traditional manufacturing culture and what younger workers want. Gen Z values comfortable work environments, fast advancement opportunities, and meaningful purpose—things often missing in conventional manufacturing settings. The challenge goes beyond attracting young talent to keeping them, as younger employees want more coaching, recognition, and flexibility than previous generations.
High talent turnover weakens the leadership bench
Even when companies successfully attract promising talent, keeping them proves difficult and undermines leadership development investments. According to data, 85% of companies say keeping high-potential employees is a major challenge, with young professionals staying only 2.2 years with employers early in their careers.
This short tenure creates a problem: companies must identify and develop leadership potential quickly, but meaningful development takes time and sustained investment. The competitive talent market makes retention harder, as growing sectors like technology and finance actively recruit manufacturing’s best performers with better development opportunities and pay packages.
Building a robust leadership pipeline: What works
Success stories from leading manufacturers reveal six proven strategies that transform talent pipelines from liability to competitive advantage in leadership in manufacturing.
Prioritize proactive succession planning and early talent identification
Effective succession planning goes far beyond emergency replacement charts to comprehensive talent mapping that anticipates future needs. Leading companies maintain detailed succession plans that identify 2-3 potential successors for critical roles, along with specific development plans for each candidate.
Finding high-potential talent early proves crucial for maximizing development return on investment. Companies like Gentherm Vietnam demonstrate this approach through systematic talent reviews that spot future leaders early in their careers, enabling targeted investment in their growth. For organizations seeking structured approaches, implementing comprehensive succession planning frameworks can provide the foundation for sustainable leadership development.
Implement a strategic “Build-Buy-Borrow-Bridge” talent framework
ManpowerGroup experts recommend the comprehensive “Build, Buy, Borrow, Bridge” framework that creates flexible, resilient leadership pipelines. This approach recognizes that no single talent strategy addresses all leadership development needs.
The four-pillar approach:
Strategy |
Focus |
Example Application |
Build |
Develop internal talent through structured programs |
Unilever’s Future Leaders Program with rotational assignments |
Buy |
Strategic external recruitment for expertise gaps |
Hiring experienced managers from competitors |
Borrow |
Utilize external expertise temporarily |
Consulting arrangements or interim executives |
Bridge |
Enable internal transitions through skill development |
Cross-functional moves and stretch assignments |
This multi-faceted approach ensures talent pipeline strength while maximizing internal promotion opportunities that boost retention. Organizations can enhance their talent identification process through strategic talent acquisition methodologies that align with long-term business objectives.
Invest systematically in targeted development and upskilling
Continuous learning forms the foundation of effective next generation leader development, requiring both technical and leadership skill enhancement. Gentherm Vietnam shows best practice through their 70:20:10 development model, where 70% of learning happens through on-the-job training, 20% through informal learning, and 10% through formal training programs.
According to Gentherm HR Manager Tran Thi Thanh Huong, “We apply the 70:20:10 model for talent development: 70% on-the-job training, 20% informal learning…and 10% formal training.” This balanced approach combines hands-on experience with structured education, creating well-rounded leaders prepared for complex manufacturing challenges.
Technical retraining becomes particularly critical as automation advances. To support systematic development efforts, organizations can implement modern performance management systems that track progress and align individual growth with business objectives.
The most effective leadership development combines real work experience with targeted training, creating leaders who understand both the technical and business sides of manufacturing. |
Design clear career pathways and foster internal mobility
Lack of clear advancement opportunities drives talent loss more than pay concerns. Successful manufacturers establish structured career progression plans that clearly communicate advancement criteria and timelines. Samsung Vietnam demonstrates this through well-defined pathways where engineers rotate through R&D, production, and supply chain roles, building comprehensive business understanding.
Internal mobility programs prove especially valuable for developing well-rounded leaders. Cross-functional rotations expose high-potential employees to different business aspects, preventing narrow specialization while building strategic thinking capabilities. Even small manufacturers can implement rotation programs by temporarily assigning future plant managers to procurement or HR functions.
Understanding compensation benchmarks becomes crucial for retention strategies. Companies can leverage comprehensive total remuneration surveys to ensure their career pathways include competitive compensation packages that retain top talent.
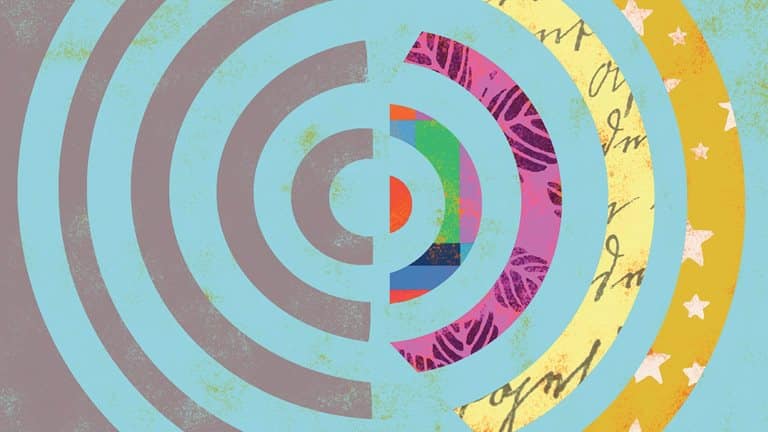
Transform your culture to attract, engage, and retain top talent
Cultural modernization becomes essential for attracting and keeping younger talent who will comprise tomorrow’s leadership ranks. Progressive manufacturers implement flexible work arrangements where possible, integrate digital collaboration tools, and create inclusive environments that value diverse perspectives.
Heineken Vietnam shows cultural transformation through their “Accelerate Your Talents” program, which includes international assignments that expose Vietnamese employees to global best practices. The company’s investment of VND 31 billion in people development during 2018 demonstrates the financial commitment required for comprehensive cultural change. Implementing comprehensive leadership training for Vietnamese manufacturing businesses can accelerate cultural transformation while building management capabilities.
Key cultural shifts for Gen Z attraction:
- Flexible scheduling options where operationally feasible
- Modern digital collaboration tools and processes
- Open communication channels and feedback systems
- Recognition programs that celebrate innovation and initiative
Addressing generational differences requires understanding diverse work styles and communication preferences. Organizations can benefit from Emergenetics assessments to enhance team dynamics and improve cross-generational collaboration.
Champion mentorship and forge strategic alliances
Formal mentorship programs provide high-impact, cost-effective leadership development that preserves company knowledge while accelerating individual growth. Toyota Vietnam’s approach of pairing senior engineers with junior colleagues transfers both technical expertise and problem-solving methods, creating well-prepared future leaders.
Strategic partnerships multiply development opportunities beyond internal capabilities. Collaborations with educational institutions like VinUniversity or industry associations provide access to specialized training while building talent pipelines from graduation forward. Organizations seeking comprehensive support can explore expert HR consulting services that provide tailored leadership development programs and proven methodologies.
Start with one mentorship pilot program pairing your most experienced managers with high-potential junior staff. Measure knowledge transfer effectiveness and scale successful approaches across the organization. |
The next generation leader development challenge facing Vietnamese manufacturers demands immediate, strategic action from CEOs who recognize that tomorrow’s competitive advantage depends on today’s talent investments. Successfully implementing next generation manufacturing investment programmes requires comprehensive succession planning, modern development frameworks, and cultural transformation initiatives. By taking decisive action now, manufacturers can build resilient leadership pipelines that drive sustained growth and competitive advantage throughout the coming decade.
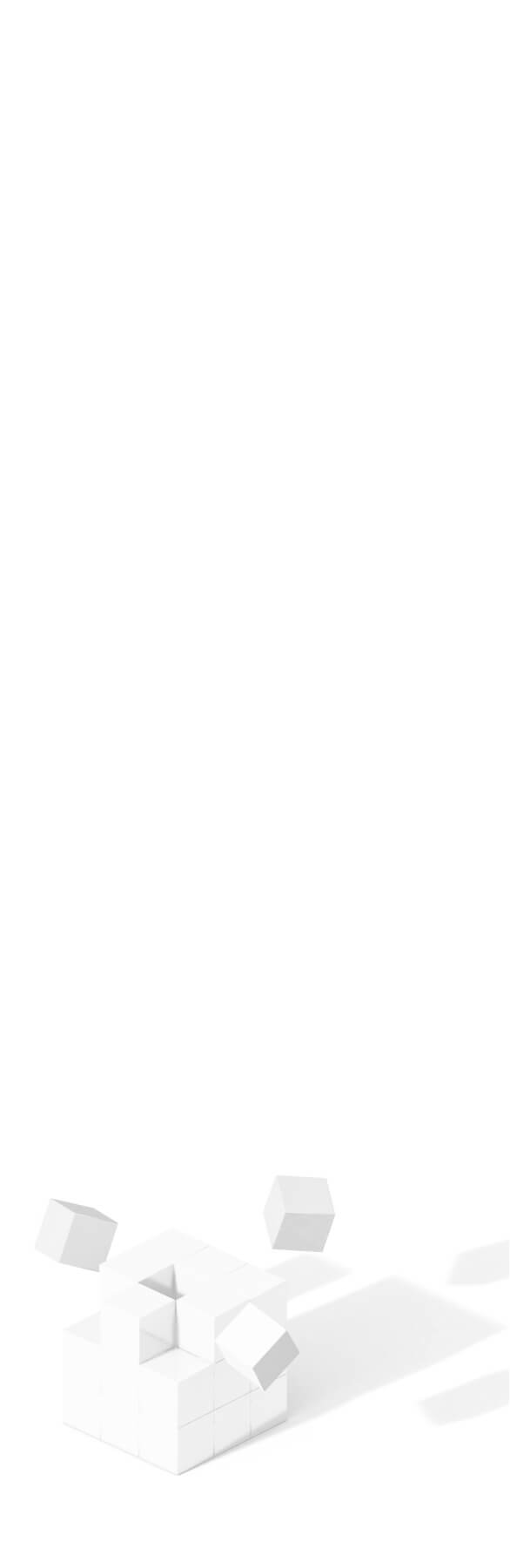
Solve your HR problems!
6th Floor, Star Building, 33 Mac Dinh Chi, District 1, Ho Chi Minh City, Vietnam