How HR Can Champion A Zero-Incident Culture In Manufacturing
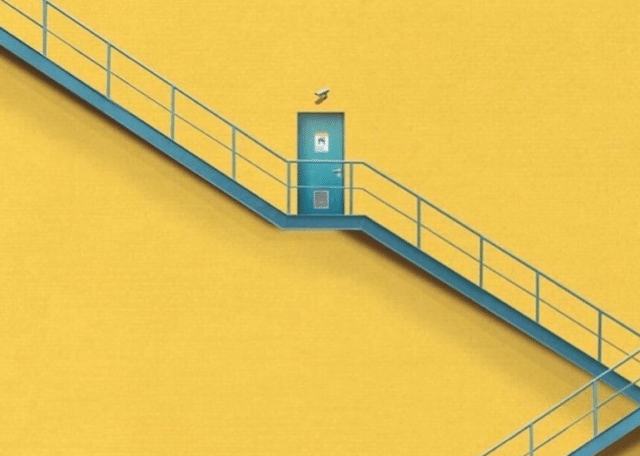
May 26, 2025
In manufacturing, workplace safety isn't just about compliance—it's a direct path to business growth and competitive advantage. Companies achieving a zero incident culture see measurable improvements in productivity, brand reputation, and bottom-line performance. For CEOs, embracing this zero incident mindset represents one of the most strategic investments available to protect and enhance business value.
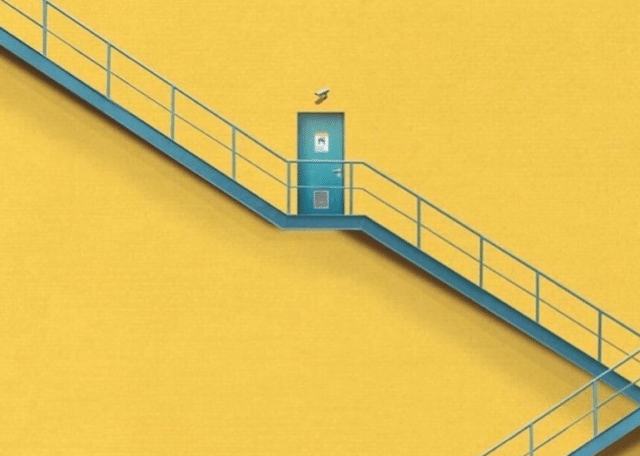
Key takeaways
- Companies with zero incident culture see direct cost savings through lower insurance premiums, reduced downtime, and fewer compensation claims while gaining competitive advantages in talent attraction and customer trust.
- HR drives safety transformation by making it a core business value, not just compliance, through comprehensive training programs and open reporting systems that prevent incidents before they happen.
- Leadership commitment from the CEO level combined with HR-driven risk management can transform safety from a cost center into a profit driver that protects both people and business performance.
A zero-incident, zero-accident culture means eliminating all workplace accidents, injuries, and near misses through prevention rather than reaction. This concept traces its roots to Philip Crosby’s Zero Defects philosophy from the 1960s and gained prominence through Japan’s Zero-Incident Campaign in 1973 and Sweden’s Vision Zero initiative in 1997, marking a fundamental shift toward embedding safety as a core operational value that drives business performance.
Why a zero-incident culture is a non-negotiable priority for modern manufacturing
The business case for zero incident safety culture has never been stronger, with mounting financial losses from workplace accidents creating urgent pressure for change while early adopters demonstrate clear competitive advantages.
Direct impact on financial performance
Workplace accidents create massive financial losses that extend far beyond medical bills. According to Vietnamese workplace safety data, economic losses from workplace accidents hit VNĐ43 trillion (US$1.68 billion) in 2024, jumping VNĐ26 trillion from the previous year. These numbers show how safety failures directly hurt profits through compensation claims, production shutdowns, regulatory fines, and higher insurance costs.
Manufacturing faces especially high risks. Property damage from workplace accidents in Vietnam exceeded VNĐ492 billion ($19.2 million) in 2024, with workers losing 154,759 total workdays. The hardest hit sectors include:
- Textiles and clothing: 14.2% of accidents
- Mining and mineral exploitation: 13.3% of accidents
- Building materials production: 10.6% of accidents
- Construction: 9.7% of accidents
These losses create ripple effects across entire supply chains, making safety a business-critical issue. Companies that achieve zero incidents see immediate cost benefits through lower insurance premiums, avoided production disruptions, and elimination of hidden costs from accident investigations and regulatory compliance issues.
Enhancing competitive advantage and brand reputation
Zero-incident performance creates real competitive advantages in talent, customers, and investor relationships. Zebra Technologies proves this point with their New Jersey plant recording over one million work hours without a lost-time accident. According to Kester Matthew, Zebra’s senior manager of environmental health and safety, “Setting standards beyond the minimum was cited as the primary reason why technology firm Zebra has recorded zero safety incidents in its manufacturing team.”
This safety record translates into business wins beyond risk reduction. Companies with strong safety performance attract better talent, win more contracts from safety-conscious customers, and get better terms from insurers and lenders. Safety excellence becomes a powerful differentiator that competitors struggle to match quickly.
Strong safety records also protect brand value in crisis situations. When accidents happen to competitors, companies with proven safety cultures maintain customer confidence and market position. This reputation shield becomes increasingly valuable as social media amplifies the reputational damage from safety failures.
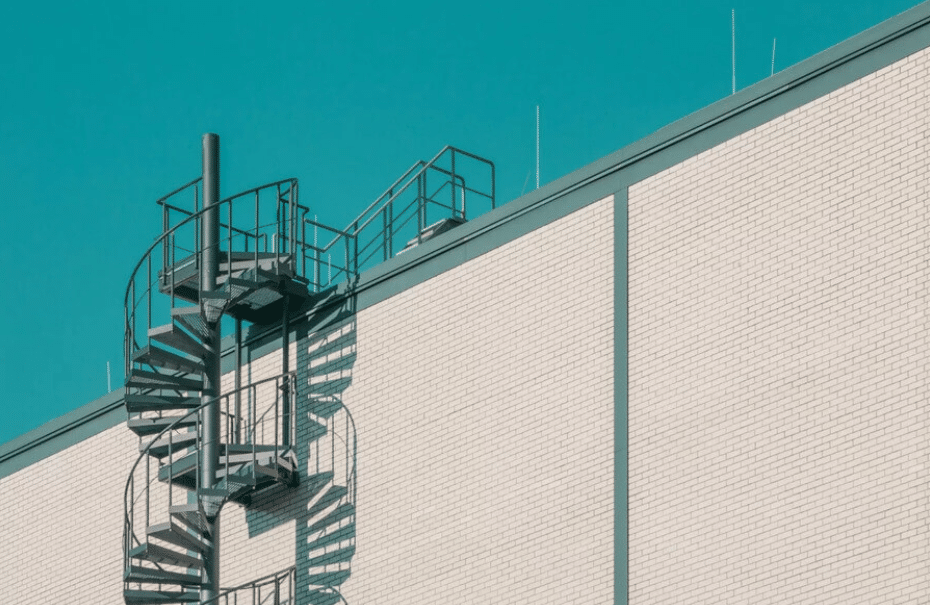
Mitigating inherent risks in manufacturing
Manufacturing environments create unique safety challenges that demand proactive management. International Labor Organization data shows Vietnam loses nearly 13,000 workers annually to workplace accidents, affecting 120,000 to 130,000 people yearly with 10 percent proving fatal. Analysis reveals that 46.9 percent of incidents stem from employer-related factors, while worker errors cause only 22.9 percent.
This data reveals a crucial insight: most manufacturing safety problems come from organizational failures, not individual mistakes. Over 90 percent of Vietnamese companies lack proper safety monitoring systems, creating vulnerabilities that good management can fix. The problem isn’t worker carelessness—it’s inadequate systems and oversight.
How HR can champion and improve a zero-incident culture in manufacturing
HR departments possess unique organizational influence that makes them natural leaders in safety transformation, combining their expertise in people management with direct access to leadership decision-making. Building this culture change in manufacturing requires strategic HR leadership at every level.
HR drives leadership commitment and embeds safety as a core value
HR’s most important role starts with making safety a top leadership priority that gets integrated into core business strategy. This follows Vision Zero’s first principle to “take leadership and demonstrate commitment,” requiring HR to ensure clear safety expectations flow from the CEO through the entire organization.
Success requires HR to position safety as a business driver, not a compliance burden. Toyota demonstrates this approach through their comprehensive safety culture spanning decades, with Safety and Health Committees established in 1938 and their STOP6 initiative launched in 1992 covering six critical accident categories. HR teams must advocate for similar long-term commitments that make safety part of organizational DNA.
This transformation demands systematic leadership development where executives model safe behaviors and allocate real resources to safety goals. Leadership training for manufacturing supervisors becomes essential for cascading safety commitment throughout the organization. HR must ensure safety performance gets built into executive compensation and strategic planning, creating accountability that drives sustained commitment.
HR spearheads proactive and continuous safety training
Effective training represents the most direct path to zero incidents, requiring HR to build comprehensive programs that create safety-first thinking while teaching proper procedures. Research shows a clear relationship between training investment and incident reduction, making education spending a direct predictor of safety performance.
HR must design training that addresses both leading indicators (factors that predict incidents) and lagging indicators (measurable results after incidents). Leading indicators include training completion rates, safety audit frequency, and near-miss reporting levels. Lagging indicators cover injury types, production shutdowns, and compensation claims. This dual approach enables continuous improvement based on performance data.
Modern training leverages technology for better results. Midwestern Contractors achieved 2,566 consecutive accident-free days by switching from paper-based safety systems to mobile devices and cloud computing, enabling real-time monitoring and rapid hazard response. HR teams should champion similar technology solutions that make safety training more engaging and immediately useful.
Training programs must also address the human psychology of risk-taking. Workers often develop dangerous shortcuts over time, especially when they don’t see immediate consequences. Effective training reinforces safe behaviors through repetition, peer accountability, and clear consequences for violations.
HR facilitates robust risk management and incident analysis
HR should champion systematic hazard identification and risk control that goes beyond quick fixes to address root organizational problems. This means implementing strong risk assessment methods and conducting thorough root cause analysis for any incidents, following Vision Zero’s principle to “identify hazards and control risks.”
The Occupational Safety and Health Administration defines root cause as “a fundamental, underlying, system-related reason why an incident occurred, that identifies one or more correctable system failures.” HR professionals must establish processes that find these underlying causes rather than just addressing immediate problems, preventing similar incidents in the future.
Risk management requires comprehensive hazard identification covering all potential harm sources, from fall risks and machinery dangers to heavy lifting injuries. HR teams should implement systematic risk assessment that evaluates both probability and severity of identified hazards, then develop targeted interventions to eliminate or control these risks before incidents occur. HR compliance frameworks provide the foundation for these systematic approaches.
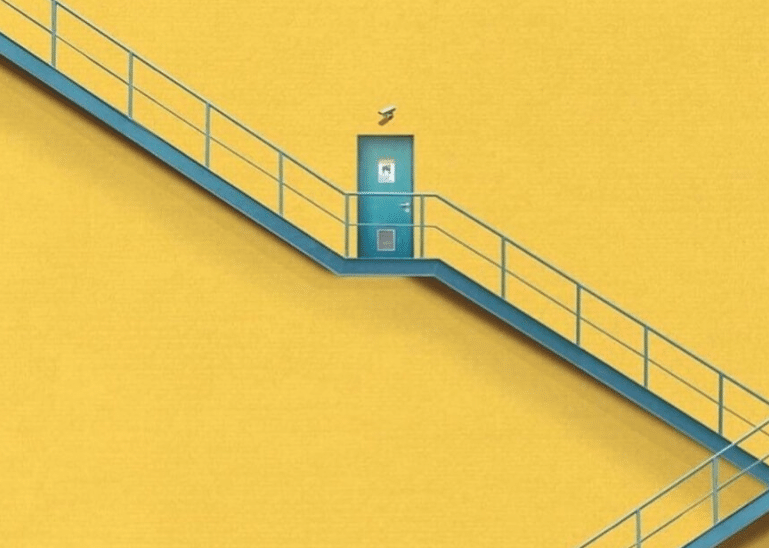
HR fosters an open culture of reporting and employee engagement
Zero-incident cultures thrive when employees feel safe reporting near misses and potential hazards without fear of blame or retaliation. HR must build this environment through clear reporting channels, active employee participation in safety initiatives, and rewards for proactive safety behaviors, following Vision Zero’s principle to “invest in people through motivational participation.”
Creating psychological safety around incident reporting requires deliberate culture change. Research shows 34 percent of workers fear retaliation for reporting incidents, undermining trust and preventing early hazard identification. HR teams must establish anonymous reporting systems and transparent communication about how reports get investigated and addressed.
Employee engagement extends beyond reporting to include active participation in safety improvements. Successful programs include safety committees with representatives from all departments, employee-led hazard identification teams, and recognition systems celebrating safety achievements. Building trust in the workplace becomes fundamental to encouraging honest safety reporting.
HR fosters an open culture of reporting and employee engagement
Zero-incident cultures thrive when employees feel safe reporting near misses and potential hazards without fear of blame or retaliation. HR must build this environment through clear reporting channels, active employee participation in safety initiatives, and rewards for proactive safety behaviors, following Vision Zero’s principle to “invest in people through motivational participation.”
Creating psychological safety around incident reporting requires deliberate culture change. Research shows 34 percent of workers fear retaliation for reporting incidents, undermining trust and preventing early hazard identification. HR teams must establish anonymous reporting systems and transparent communication about how reports get investigated and addressed.
Employee engagement extends beyond reporting to include active participation in safety improvements. Successful programs include safety committees with representatives from all departments, employee-led hazard identification teams, and recognition systems celebrating safety achievements. Building trust in the workplace becomes fundamental to encouraging honest safety reporting.
For CEOs, championing a zero-incident, zero-accident culture represents a direct investment in organizational strength, profitability, and long-term competitive advantage. HR leaders, whether internal or supported by specialized HR outsourcing services, serve as crucial partners in this transformation, converting safety from a compliance requirement into a deeply embedded cultural value that drives business performance. Building a strong manufacturing culture requires sustained commitment and systematic implementation. The time to empower HR teams and build safer, more productive manufacturing environments is now.
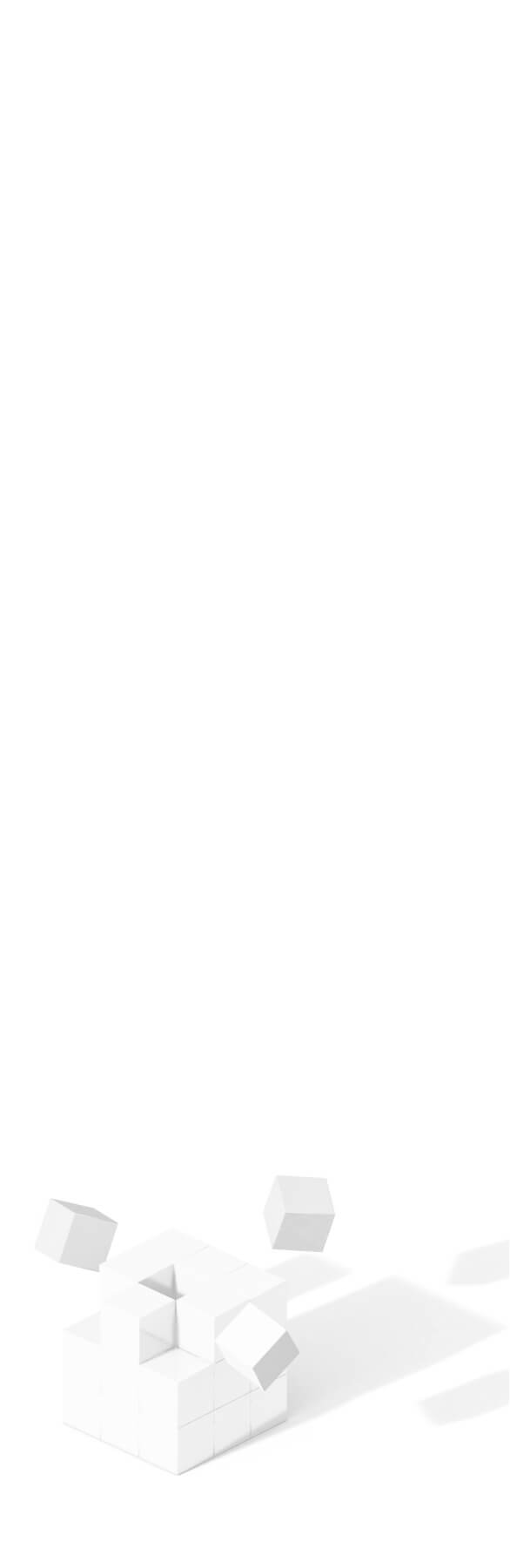
Solve your HR problems!
6th Floor, Star Building, 33 Mac Dinh Chi, District 1, Ho Chi Minh City, Vietnam