From Compliance To Culture: How HR Can Transform Manufacturing Workplace Engagement
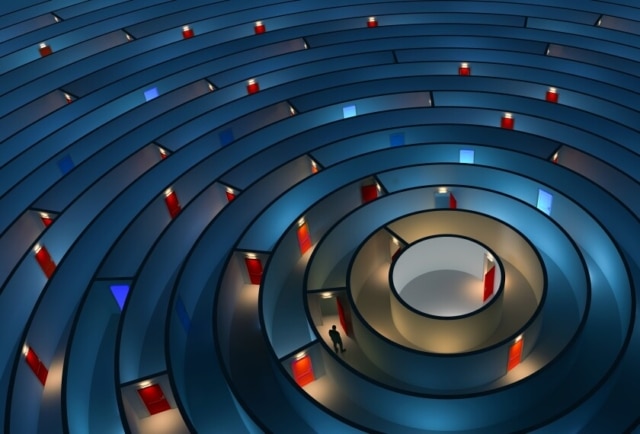
May 20, 2025
Culture change in manufacturing has transformed how HR operates. It's no longer just about enforcing rules and avoiding penalties. Leading companies now use safety protocols and work standards as building blocks for powerful company cultures that drive better results, higher engagement, and long-term growth.
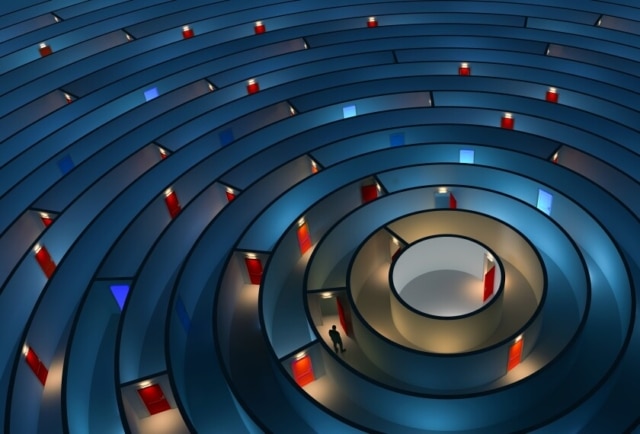
Manufacturing HR traditionally focused on compliance—ensuring legal requirements, safety protocols, and procedures were followed exactly. Today’s most successful manufacturing transformation leaders recognize these same foundations can transform workplace dynamics entirely, turning basic administration into a strategic driver of worker engagement, trust, and measurable business results.
The old way when compliance was just about rules
Manufacturing’s compliance-first era created necessary order but also built significant barriers that smart leaders now recognize as limits to growth.
Keeping order and safety first
Early manufacturing HR built its foundation through strict rule enforcement. This compliance-first approach brought essential order and consistency to factory floors. When companies applied fair policies and safety rules consistently, they created basic trust. Workers saw that companies valued their well-being through protective measures. Strong HR compliance connected directly to fairness, consistency, and transparency—elements that experts identify as key building blocks of strong manufacturing culture. This systematic approach planted important seeds of trust and safety that positive cultures could later grow from.
The problem with only rules
However, a purely compliance-driven approach revealed serious engagement problems. According to a 2025 safety industry white paper, simply meeting minimum regulations often resulted in minimal employee engagement in the manufacturing industry. The report found that compliance rarely encourages worker participation in safety decisions, leading to disengagement and unsafe behaviors. Workers followed rules mainly from obligation or fear of discipline, without genuinely believing in the standards behind those rules. This created what researchers call a “checklist mentality”—doing the minimum required rather than caring about real improvement.
Understanding the importance of HR compliance becomes crucial when organizations realize that well-structured policies can serve broader cultural purposes beyond mere legal protection.
The high cost of low interest
This narrow compliance focus created chronically low engagement levels with real business costs. According to the Manufacturing Institute, only 25% of manufacturing employees actively engage in their work. Poor engagement creates serious problems. Talentnet survey data shows companies with low engagement experience 81% higher absenteeism and 41% more quality defects compared to companies with better engagement levels. These numbers prove that a compliance-only approach, without culture strategy, leaves workers uninterested and disconnected, ultimately hurting both performance and quality.
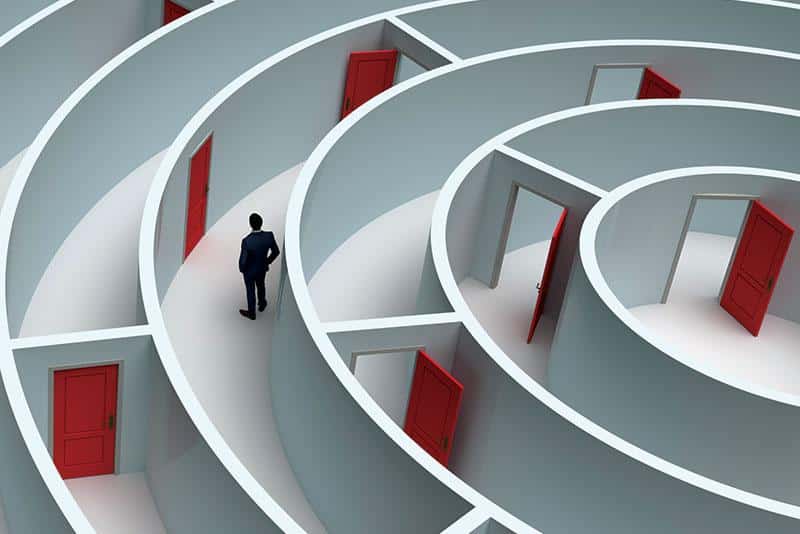
How can HR make compliance a real cultural win in manufacturing?
Smart manufacturing transformation leaders transform routine compliance activities into powerful culture-building tools through strategic thinking and employee empowerment. This shift requires moving beyond checkbox mentality to genuine engagement.
HR uses legal safety rules to show genuine care for well-being
Progressive manufacturers move beyond simply posting safety signs to meet regulations. Instead, they encourage employee-driven safety committees, open reporting of hazards, and recognition for safe behaviors. This creates what research identifies as a proactive safety culture where everyone takes ownership.
According to the Journal of Occupational and Organizational Psychology, a strong workplace safety climate positively affects employee engagement. Workers who feel their organization truly cares about their well-being show higher energy, motivation, and enthusiasm. One survey of over 6,000 truck drivers proved this connection. Drivers with positive views of their company’s safety climate reported higher job satisfaction and engagement, while those who saw poor safety climates showed higher turnover rates. This demonstrates that safety programs can evolve into genuine cultural strengths that improve morale and retention.
Organizations seeking comprehensive Vietnam business compliance services often discover that robust compliance frameworks naturally support stronger employee engagement when implemented thoughtfully.
HR turns fairness and equality laws into a culture of belonging
Leading companies transform basic anti-discrimination compliance into comprehensive inclusion strategies. Rather than treating diversity as a legal checkbox, manufacturers embed inclusion into daily operations. HR experts note that following laws on fair treatment, equal opportunity, and safety shows commitment to employees’ welfare and can positively impact workplace culture, employee morale, and turnover rates. When workers feel valued, respected, and protected, they become significantly more engaged, productive, and loyal.
The organizational culture transformation requires understanding how Gen Z values workplace HR transformation, as newer generations expect more inclusive and purpose-driven work environments.
HR links skill compliance and safe operations to career growth
Smart HR departments connect mandatory skill standards and safety requirements directly to advancement opportunities. Instead of treating competency requirements as mere operational necessities, they design clear pathways showing how learning new skills, working safely, and following best practices can lead to promotions and expanded opportunities. This approach gives employees compelling reasons to invest in their development while simultaneously meeting compliance objectives.
Implementing benefits of well-defined HR policies creates the structural foundation necessary for linking compliance excellence to career advancement opportunities.
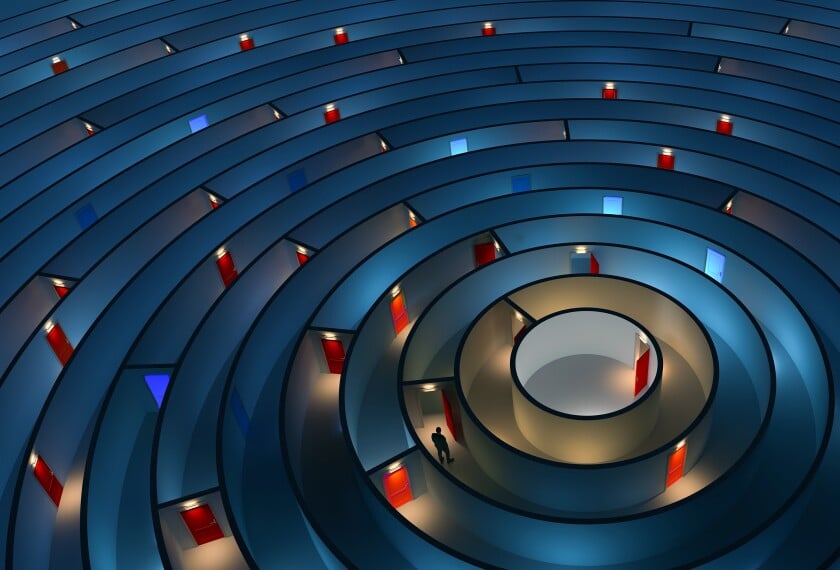
HR uses ethical codes and conduct rules to attract and keep good people
Companies build organizational reputation for integrity and stability by consistently upholding codes of conduct and managing risks related to unethical behavior. Several global manufacturers demonstrate how this organizational culture transformation works in practice.
Compliance excellence and cultural strength reinforce each other. Strict standards supported by employee empowerment create competitive advantages that extend far beyond regulatory requirements. |
Toyota exemplifies this approach perfectly. Their production system relies on strict standards for quality and safety, supported by cultural principles like “respect for people” and continuous improvement. At Toyota’s manufacturing units, safety and health compliance involves committees that include labor union representatives, signaling that safety represents shared responsibility rather than top-down mandates. According to the British Safety Council, Toyota’s systematic, people-centered safety culture yields multiple benefits including higher morale and engagement, fewer accidents, and stronger overall performance.
General Motors provides another compelling transformation example. In 1994, GM started an enterprise-wide safety culture transformation across 160 North American plants, moving from rules-driven approaches to personal ownership and transparency. GM’s leadership recognized that their top-down compliance approach needed fundamental change, starting with senior executives. Through workshops and behavioral modeling, leadership demonstrated safety-first mindsets throughout the organization. This systematic implementation turned a previously compliance-centered program into a unifying cultural mission, resulting in lasting injury reductions and an empowered workforce willing to speak up about safety concerns.
Unilever further illustrates compliance-to-culture evolution through their “Vision Zero” safety program. According to Unilever’s Group Safety Director, “You cannot have holistic, responsible growth unless you care about people, and that means making sure those people go home safely every day.”
This leadership stance frames safety rules as expressions of genuine employee care. In Unilever’s factories, safety briefings evolved from top-down reminders into interactive discussions where workers voice concerns and nominate peers for safety excellence. By embedding safety into daily routines and empowering universal ownership, Unilever transformed compliance mandates into unifying cultural elements.
CEOs must recognize HR’s compliance work as a strategic investment in organizational culture in manufacturing industry strength, not merely a cost center. According to Gallup data, business units with high employee engagement report 70% fewer safety incidents, while engaged frontline workers are 78% safer and 44% more profitable than their disengaged counterparts. Leaders who champion culture-driven compliance create sustainable competitive advantages through workforce excellence.
To begin your culture transformation roadmap, consider conducting an Employee Engagement Snapshot Survey to establish baseline metrics and identify specific areas where compliance programs can become culture-building opportunities.
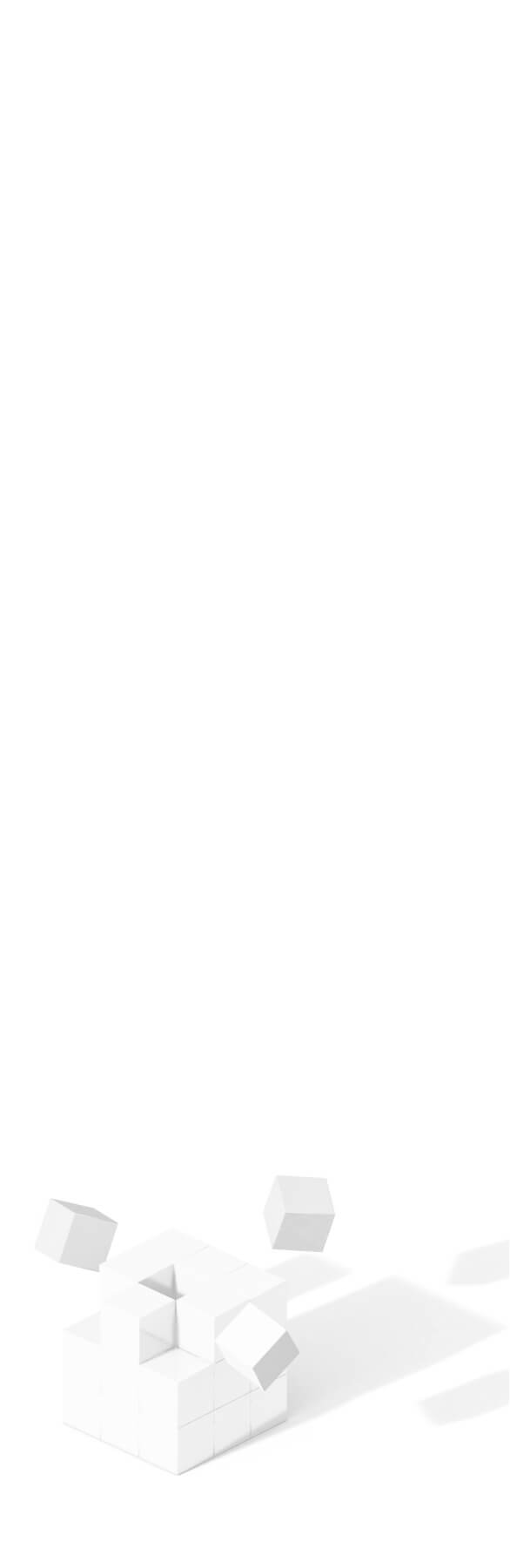
Solve your HR problems!
6th Floor, Star Building, 33 Mac Dinh Chi, District 1, Ho Chi Minh City, Vietnam