Why Connected Worker Manufacturing Transforms Vietnam's Talent Retention Crisis
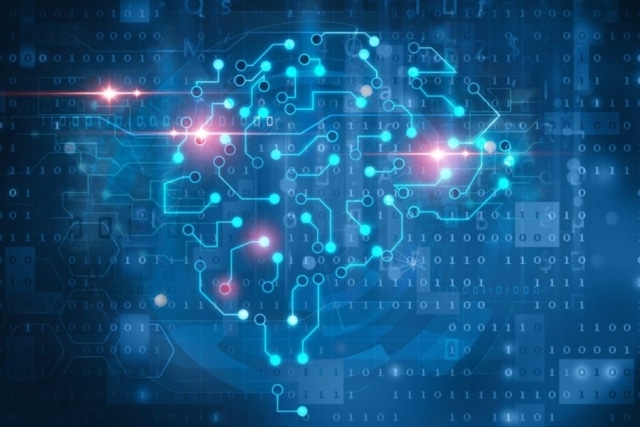
May 22, 2025
Vietnam's connected worker manufacturing sector is hemorrhaging talent and profits. With turnover rates hitting 24% industry-wide and climbing to 36% in labor-intensive sectors, factories face a relentless cycle of recruitment and training costs. 65% of manufacturing companies now identify employee retention as their biggest challenge. Each worker who leaves costs 3-5 months' wages to replace, creating financial drain that threatens competitiveness. However, a game-changing solution is emerging: the connected worker mindset, where digital tools empower employees and transform workplaces into environments people want to stay in.
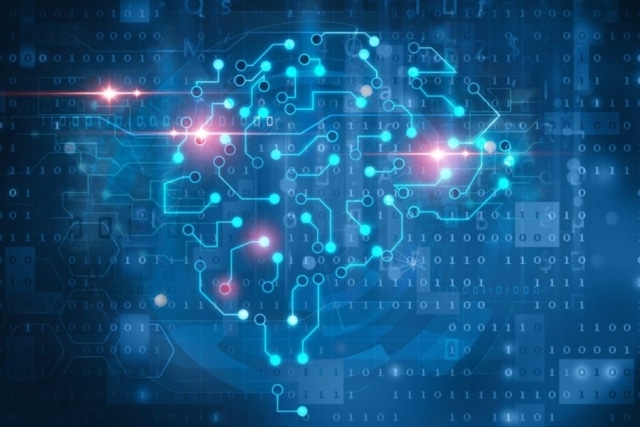
Key takeaways
- Vietnam’s manufacturing sector faces a 24% average annual turnover rate, costing companies 3-5 months’ wages to replace each departing worker and creating ongoing operational instability.
- Connected worker strategies deliver measurable results, with companies reporting 17% productivity increases, 40% faster employee onboarding, and up to 70% lower turnover rates.
- This approach transforms workplaces by offering digital skills training, improving safety conditions, and creating modern environments that appeal to younger workers who currently avoid manufacturing jobs.
- Investment in connected worker manufacturing technology represents a strategic business decision that improves both employee retention and operational efficiency, directly impacting profitability.
High employee turnover and skills shortages pose serious business risks for Vietnamese manufacturers. While most companies focus on reactive hiring and basic pay adjustments, smart leaders are adopting a connected worker manufacturing approach that solves retention problems while boosting productivity and creating sustainable competitive advantages.
What is the connected worker mindset?
The foundation of successful talent management in the manufacturing industry lies in understanding how technology can transform the fundamental nature of manufacturing work, moving beyond traditional models to create empowered, digitally-enabled workforces.
Manufacturing is changing fast. Manufacturing’s modern workforce mindset reveals how old-style top-down management is giving way to workplaces where employees use technology to work smarter, communicate better, and solve problems faster. What is connected worker technology? It means giving frontline employees digital tools that help them do their jobs better. According to industry research, this approach uses internet-connected sensors, mobile devices, and cloud computing to connect workers with machines, processes, and colleagues. Instead of replacing human workers, these tools make them more capable and confident.
This transformation rests on six fundamental pillars that work together to create a more engaged and productive workforce:
- Digital access: Workers use tablets and mobile devices to access real-time work instructions, troubleshooting guides, and expert support at their workstation
- Cross-team communication: Instant messaging and digital platforms break down department silos, enabling faster problem-solving across shifts and management levels
- Sensor-driven insights: IoT sensors on equipment provide continuous monitoring data that helps workers respond proactively to maintenance needs and process variations
- Streamlined workflows: Digital processes and augmented reality guidance reduce task completion time and minimize errors, with Accenture research showing 30% productivity improvements
- Enhanced safety protocols: Smart devices deliver real-time hazard alerts and visual safety instructions directly to workers’ field of view
Knowledge capture: Digital platforms preserve expert knowledge from experienced workers and deliver it to new employees through interactive training modules.
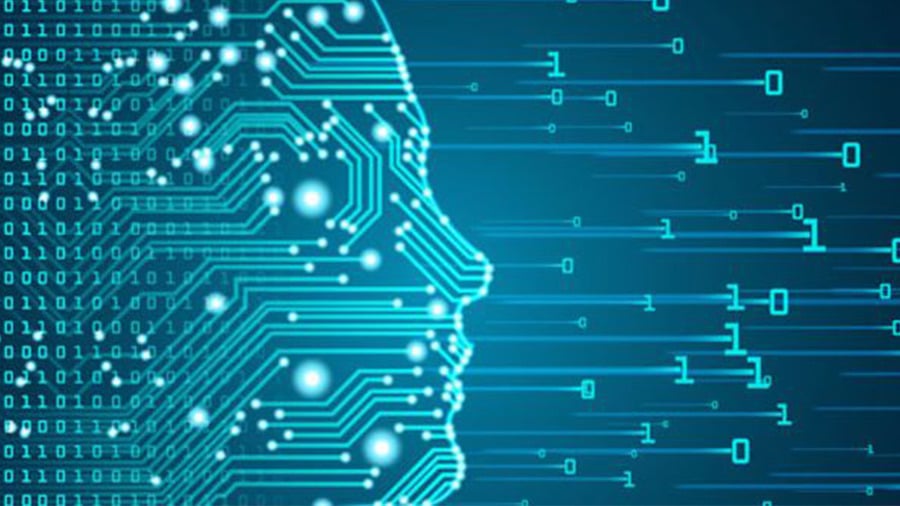
Why a connected worker strategy helps attract and keep your employees
The business case for connected worker strategy becomes clear when examining how they directly address the specific motivations and concerns driving Vietnamese workers’ employment decisions.
Vietnamese workers have specific needs and expectations that directly affect whether they stay or leave. Research shows what drives employee loyalty in Vietnam’s manufacturing sector, and connected worker strategies address these key areas effectively.
Offers better skills and career paths
Skills development is a powerful tool for keeping employees, especially important given Vietnam’s training challenges. According to the Ministry of Planning & Investment, nearly 77% of Vietnam’s workforce lacks technical qualifications. Connected worker platforms enable continuous learning through:
- Interactive modules accessible during shifts
- Augmented reality training for complex tasks
- Micro-learning apps for skill building
- AI-driven training recommendations
Companies using digital training see dramatic improvements in employee confidence and skills. A battery manufacturer using AI-driven connected worker platforms achieved 40% faster onboarding while boosting productivity by 17%. This faster skill development improves operations and shows employees the company invests in their growth.
LinkedIn research shows employees are 75% more likely to stay at companies that invest in continuous training. For Vietnamese manufacturers competing for skilled workers, this investment creates a significant advantage in both recruiting and keeping talent.
Creates safer and better working conditions
Workplace safety directly affects employee satisfaction and retention, especially in manufacturing where physical risks are real. Connected worker technologies provide real-time safety monitoring through wearable devices, instant hazard reporting, and predictive analytics that spot potential problems before accidents happen.
Digital tools simplify complex safety procedures with visual guidance and automatic compliance checking. Workers with smart devices get immediate alerts about environmental hazards, equipment problems, or procedure violations. This proactive safety approach shows management cares about employee wellbeing while reducing the stress that comes with high-risk manufacturing work. Implementing strategies to improve mental health in the workplace becomes more effective when supported by technology that reduces job-related stress and anxiety.
Companies implementing connected safety solutions report measurable improvements in both accident reduction and employee morale. When workers feel protected and supported by technology, they trust their employer more and feel more confident in their daily work.
Builds stronger communication and a positive culture
Poor communication is a major cause of employee dissatisfaction in Vietnamese manufacturing. Inadequate communication creates “unhappy and unproductive workplaces” that drive high turnover and constant hiring.
Connected worker platforms solve this by creating clear communication channels between management and frontline employees. Digital displays show real-time production metrics, safety achievements, and employee recognition, while mobile apps let workers provide feedback, report issues, and access company information. This transparency helps workers understand how their work affects business success.
Research shows engaged manufacturing teams have 70% lower turnover than disengaged groups. By enabling open communication and regular recognition, connected worker systems align with current culture trends for manufacturing companies that modern employees, especially younger workers, expect. Understanding the importance of culture-fit in talent acquisition becomes crucial when implementing connected worker initiatives that reshape organizational culture.
Boosts efficiency, supporting fair compensation
Better efficiency from connected worker systems creates the financial foundation for competitive pay packages. When workers have access to real-time information, digital work instructions, and immediate expert support, they work faster and make fewer mistakes. Accenture research confirms connected workers improve productivity by 30%, creating measurable value that supports investment in employee compensation and benefits.
This efficiency improvement addresses the main concern of Vietnamese workers. Research shows 58.7% prioritize salary and benefits above everything else. Connected worker technologies help companies improve productivity while maintaining or improving worker satisfaction, creating a sustainable model for competitive compensation. Developing a fair salary structure becomes more feasible when productivity gains from connected worker initiatives provide the financial foundation for competitive wages.
The productivity gains also reduce overtime requirements and work-related stress, improving work-life balance while meeting operational targets. This dual benefit of higher efficiency and better working conditions directly addresses what Vietnam’s manufacturing workforce wants. Companies can also leverage these improvements to offer attractive employee benefits that further enhance retention.

Empowers workers and reduces job stress
Access to information is critical for job satisfaction and stress reduction. Traditional manufacturing often leaves workers feeling isolated and dependent on supervisors for basic problem-solving. Connected worker systems provide instant access to troubleshooting guides, quality standards, and expert consultation, enabling independent decision-making and problem-solving.
This empowerment changes the worker experience from reactive task completion to proactive process improvement. Workers with real-time data and digital support tools report higher job satisfaction and greater confidence in their abilities. Reducing frustration when workers can solve problems independently creates a more positive and engaging work environment.
A paper manufacturer implementing connected worker onboarding reduced new hire turnover from 94% to significantly lower levels by providing digital guidance and support systems. This shows how technology can address the basic stress factors that drive employees to look for other jobs.
Makes your factory a modern, desirable workplace
Employer reputation is increasingly important for attracting talent, especially as younger generations enter the workforce. The World Economic Forum notes that 70% of young workers avoid manufacturing jobs due to perceptions of outdated working conditions and limited growth opportunities.
Connected worker technologies signal a company’s commitment to modernization and employee development. Factories with digital tools, mobile applications, and data-driven processes appeal to tech-savvy workers who expect modern technology in their workplace. This technological sophistication sets progressive manufacturers apart from competitors still using paper-based processes and old communication methods.
For Vietnamese manufacturing leaders, adopting a connected worker manufacturing strategy is both a strategic necessity and a competitive opportunity. Evidence clearly shows that companies investing in digital worker empowerment achieve measurable improvements in retention, productivity, and efficiency. This goes beyond HR initiatives to fundamental business strategy that positions manufacturers for sustainable success in an increasingly competitive global market.
Implementing connected worker strategy requires specialized expertise in talent management in the manufacturing industry. Professional HR consulting services can help accelerate this transformation and ensure successful implementation while addressing the unique challenges of Vietnam’s manufacturing sector.
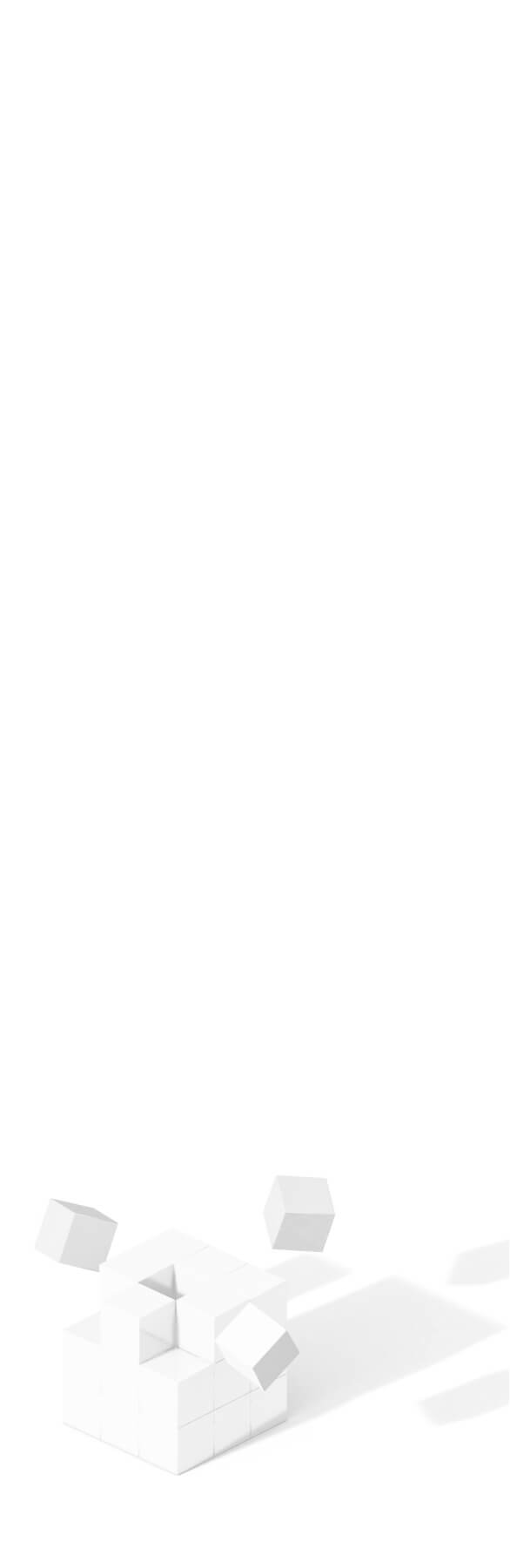
Solve your HR problems!
6th Floor, Star Building, 33 Mac Dinh Chi, District 1, Ho Chi Minh City, Vietnam