Why HR in Manufacturing Is The Missing Link In Your Lean Transformation
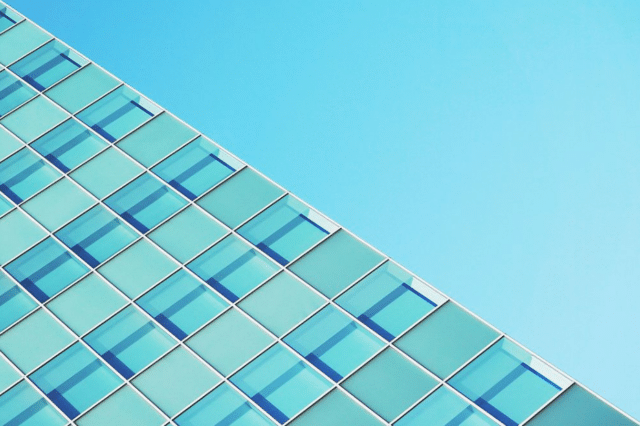
May 21, 2025
Many companies miss out on lean manufacturing's potential for 40%+ productivity boosts because they treat it as a purely operational initiative. Traditional HR systems often create the barriers that prevent lean transformation from taking root. When HR in manufacturing rewards individual performance over teamwork, or when hiring doesn't focus on problem-solving skills, what should be a strategic opportunity becomes an exercise in pushing against organizational resistance. Companies that succeed discover HR isn't just a support function—it's what makes lean transformation possible.
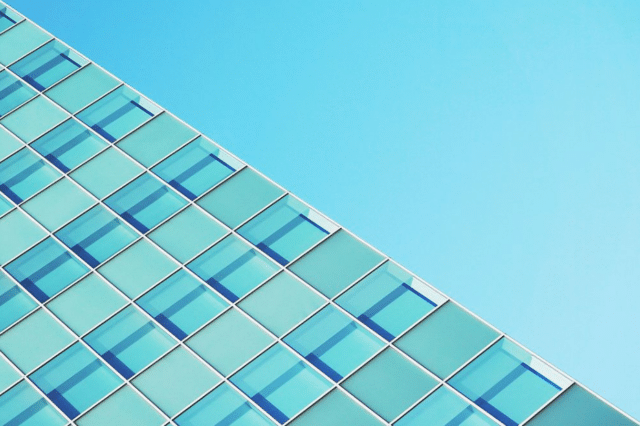
Key takeaways
- Companies that align HR strategy with lean manufacturing achieve productivity gains exceeding 40% without major capital investment.
- Manufacturing faces a talent crisis costing up to $40,000 per skilled worker replacement, creating barriers to lean success
- Strategic HR involvement—from hiring problem-solvers to building improvement cultures—directly drives profitability and competitive advantage.
- Organizations where HR partners with operations from day one see remarkable results, with some achieving massive market value increases over time.
Achieving sustained lean manufacturing results depends on strategic HR in manufacturing involvement, transforming human resources from a potential barrier into the primary success driver. While lean’s tools are well-documented, the people systems that make those tools effective determine whether transformation succeeds or fails.
Lean transformation: a powerful untapped opportunity
Despite decades of proven results, lean manufacturing remains one of business’s most underused competitive advantages. According to an Industry Reimagined 2030 survey, only 10–15% of companies systematically apply lean principles to gain full benefits. This implementation gap represents a major strategic opportunity for forward-thinking leaders.
Companies that fully commit to lean transformation see remarkable returns. Among organizations that embrace lean methodologies, 74% report productivity gains exceeding 40% without heavy capital investment. These aren’t marginal improvements requiring massive infrastructure spending—they’re efficiency gains achieved through:
- Better processes and workflow optimization
- Reduced waste across all operations
- Enhanced worker engagement and empowerment
The math is compelling for any CEO evaluating growth strategies. When three-quarters of committed organizations achieve such substantial productivity improvements, the question becomes why so few companies successfully implement lean. The answer increasingly points to workforce challenges that operational approaches alone cannot solve.
What workforce issues stop lean?
The manufacturing talent landscape has shifted dramatically, creating fundamental HR challenges in manufacturing industry that make even the best lean strategies difficult to execute.
High staff turnover creates immediate barriers to sustainable improvement. According to industry data, U.S. manufacturing experienced 4.7 million worker departures in 2023—approximately one-third of the entire sector’s workforce. This constant churn prevents the knowledge building and process refinement that understanding lean transformation methodologies require.
Skills gaps present an equally significant obstacle. In Vietnam, as of 2023, only 27% of workers possessed degrees or training certificates, leaving approximately 38 million workers without formal skills training. This skills shortage makes it difficult for firms to implement lean methods that require sophisticated problem-solving capabilities and process understanding.
Manufacturing leaders recognize these challenges as threats to growth. Nearly 60% of manufacturers surveyed in Q3 2024 cited inability to attract and retain employees as their top challenge for business success—ranking ahead of revenue growth concerns.
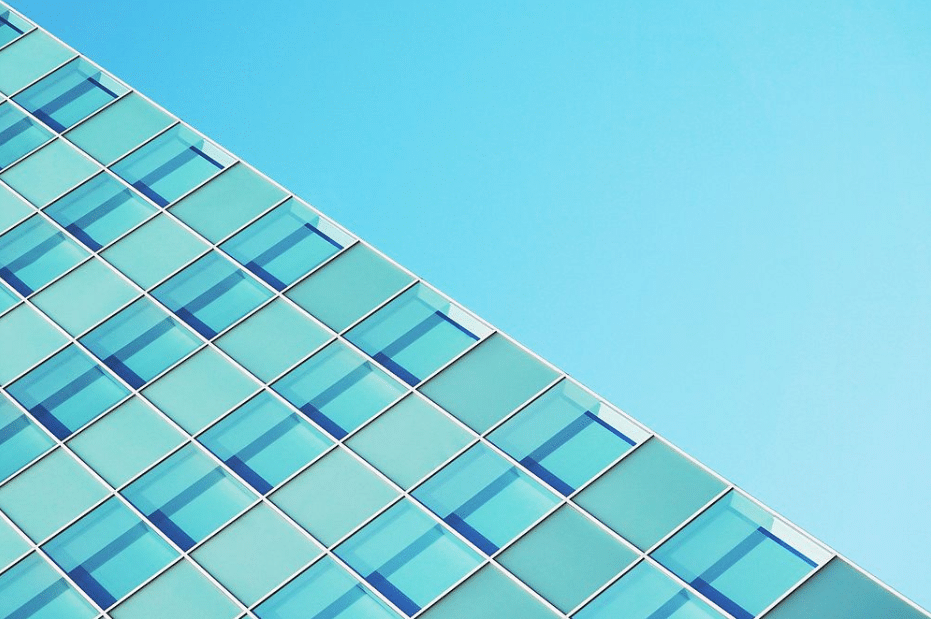
How can HR drive lean success?
Smart manufacturers are discovering that HR departments hold the key to unlocking lean’s full potential through four strategic interventions that directly address workforce barriers and deliver manufacturing HR support.
Fit lean into talent plans
HR must restructure talent management systems to support lean principles rather than undermine them. This requires shifting hiring criteria from purely technical skills to include problem-solving abilities and collaborative mindsets essential for continuous improvement.
Traditional performance systems often reward individual output and firefighting behaviors that directly conflict with lean’s emphasis on systematic improvement and teamwork. Lean coach Kathi Hanley warns that “employee selection, compensation, promotion, and retention practices—all typically in HR’s wheelhouse—need to support the transformation to a lean enterprise. Often we see traditional HR systems failing to promote the behaviors needed for lean.”
Organizations achieving lean success take specific actions through strategic human resource management:
- Redesign promotion pathways to value leadership in improvement projects
- Incorporate lean behaviors into performance evaluations
- Adjust compensation plans to include team bonuses for quality targets
- Update job descriptions to emphasize continuous improvement responsibilities
Train staff for real gains
HR-led training programs become the foundation for sustainable lean transformation. Comprehensive skill-building initiatives must address both technical lean methodologies and the cultural mindset changes required for sustained success.
A mid-sized Vietnamese machining company demonstrates the transformative potential of strategic training investment. With HR support for lean practices implementation and employee development, the organization achieved operating profit increases of 50%, labor productivity improvements of 25%, and machine productivity gains of 15%. The company also implemented a leadership training roadmap that qualified multiple project managers and improved leadership capability scores by 25%.
Nike’s global lean supply chain initiative provides another compelling example of training-driven results. By establishing a dedicated lean training center in Vietnam and involving HR and training teams in educating both factory managers and Nike staff, the company achieved systematic adoption across its supply base. As a result, 80% of Nike’s footwear manufacturing partners adopted Nike’s lean production system, leading to increased productivity, reduced defect rates, and shortened product lead times.
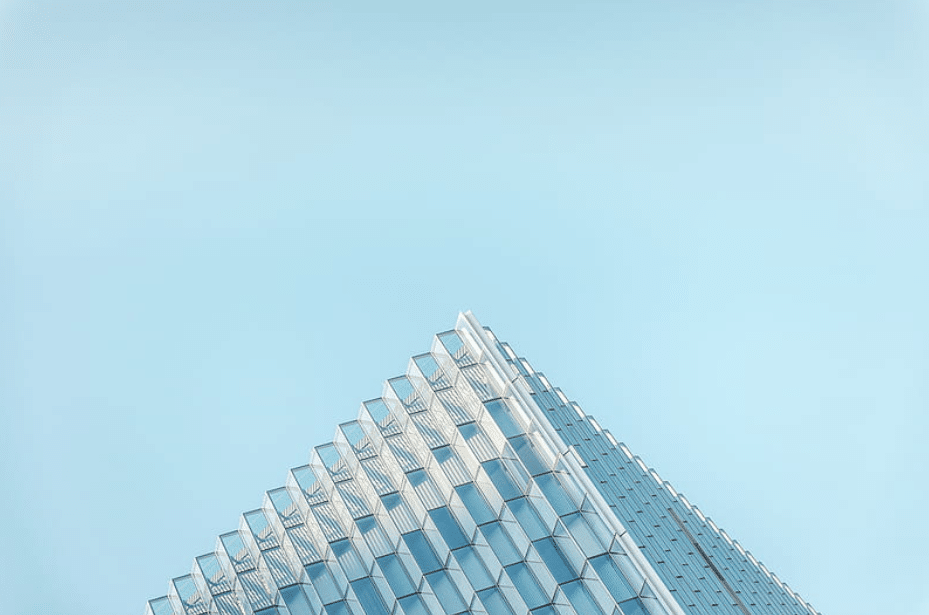
Build a lean culture for lasting edge
Cultural transformation represents perhaps HR’s most critical contribution to lean success. According to a 2024 Gartner survey, over half of HR professionals identify organizational cultural resistance to change as one of the biggest challenges to achieving strategic priorities.
This resistance becomes particularly problematic in lean transformations, which require fundamental shifts in how employees approach problem-solving and collaboration. Creating sustainable behavior change requires addressing the underlying beliefs and practices that undermine improvement initiatives.
Danaher Corporation exemplifies the long-term value of HR-driven culture building. The company’s Danaher Business System, built on continuous improvement principles, systematically integrated over 50 acquisitions through HR-reinforced lean behaviors. This approach contributed to approximately 30% annual profit growth and an 80,000% increase in market valuation since the 1980s. The sustained competitive advantage came from aligning talent development with process excellence, creating an organizational capability that competitors could not easily replicate.
Make HR and operations partners
Successful lean transformations require HR involvement from initial planning stages rather than post-implementation support. This partnership approach ensures people-related considerations inform all major operational decisions.
CEO Suhail Bin Tarraf, who led a large-scale lean turnaround, emphasizes that “it was hard to overestimate the need for HR support at every level. It really was crucial to the transformation’s success.” This reflects the integrated approach required for sustainable change.
Practical partnership involves HR leaders participating in lean steering committees and co-owning transformation roadmaps. When production processes undergo redesign, HR assesses impacts on job roles and works with supervisors to redefine responsibilities. During lean-driven restructuring, HR provides change management guidance and communication strategies to minimize workforce disruption.
Monitoring organizational pulse throughout transformation allows early intervention when engagement or understanding gaps emerge. Joint HR-Operations updates to senior leadership should cover both technical metrics and people metrics, ensuring balanced progress assessment.
To capture lean manufacturing’s full potential, CEOs must position HR in manufacturing as a strategic transformation partner rather than a support function. Lean success fundamentally depends on workforce engagement, capability development, and cultural alignment—all areas where HR expertise directly impacts business outcomes. Organizations seeking comprehensive HR consulting support can accelerate their lean transformation journey by addressing both operational and people challenges simultaneously. The evidence is clear: ignoring HR’s role in lean transformation means leaving substantial productivity gains and competitive advantages unrealized.
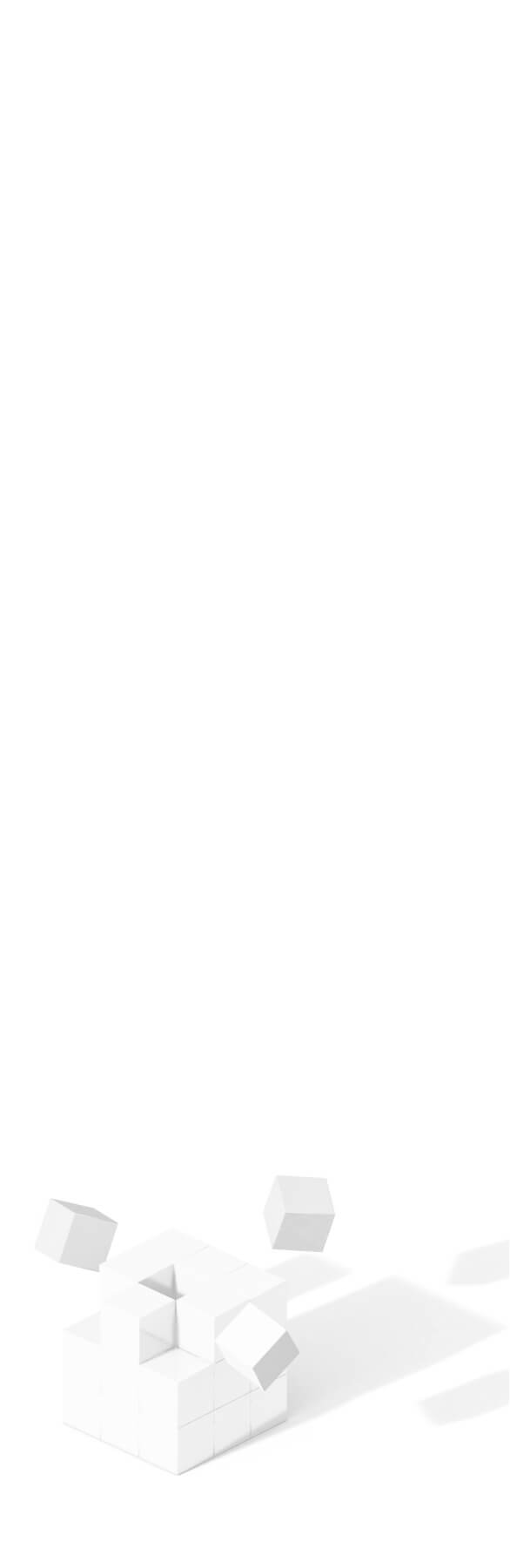
Solve your HR problems!
6th Floor, Star Building, 33 Mac Dinh Chi, District 1, Ho Chi Minh City, Vietnam